润滑油企业生产计划管理系统的构建
润滑油企业就是典型的离散型订单驱动式的生产企业,虽然润滑油企业通过M ES系统和ERP系统已经获得了极强的生产过程管控能力,但在实际的生产计划排程中还是依靠调度员的个人经验来进行离线操作,影响了计划的及时性和准确性 。APS智能排产系统通过优化计划管理、原料需求 、成本核算、数据管理等功能,将订单需求转化成生产任务,同时与MES系统、ERP系统、LIMS系统、DCS系统以及在线工控机进行交互,并综合考虑储罐及生产线资源的占用情况、工序间的依赖关系,为调度员提供更加方便、直观的排程工具,实现智能化排程管理和任务的全过程跟踪。
润滑油生产需要充分考虑质量、原料、设备、人员和时间等因素。因此,本设计是基于企业原有的MES系统和ERP系统建立APS系统排程,接入企业原有的数据库进行交互,主要规划了计划管理、工厂模型管理、生产过程管理、质量管理、看板管理等生产管理模块,最终实现“ERP计划 — APS排程 — MES执行— ERP发运”的生产全过程覆盖的信息化管理。
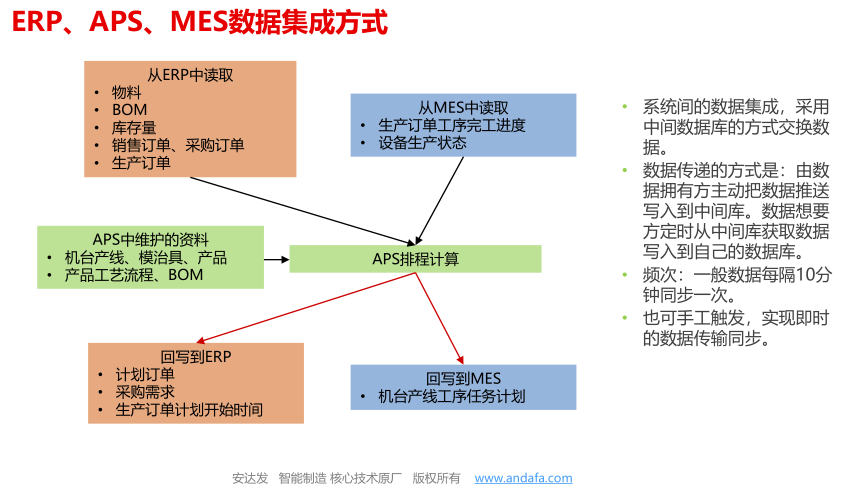
安达发APS计划排产系统主要功能
计划管理 :计划管理又分成需求计划、生产计划,通过APS系统的需求识别,计划人员可以看到 每个需求对应的计划到货时间,结合系统生成的排程甘特图推出原材料的最迟到货时间,减少了计划人员和采购人员的人工干预,大幅提高了操作的便捷性和准确性。此外 ,供应商和承运商也可以根据原材料需求同步安排自己的交货及生产计划,实现JIT式的采购与送货计划。在实际生产过程中,APS系统还需要根据一定的规则,确定每个订单的排产次序。排序的规则包括:
- 客户的优先级,客户级别高的订单优先排产;
- 交货时间的优先级,交货周期短的订单优先排产;
- 效益的优先级,获得效益最高的订单优先排产;
- 欠量时间的优先级,对于欠量时间长的订单优先排。
任务分配 :APS系统在完成计划输出及订单排序后,需要将具体的任务按照订单的优先顺序分配至生产装置,并根据分配的顺序生成任务甘特图。
计划分析:在当前生产任务完成后,需要将任务的实际的开始时间与结束时间和任务的计划开始时间与结束时间进行比较,查找差距的原因,并分析主要的影响生产因素,指导实际生产的持续优化,形成计划业务的闭环管理。
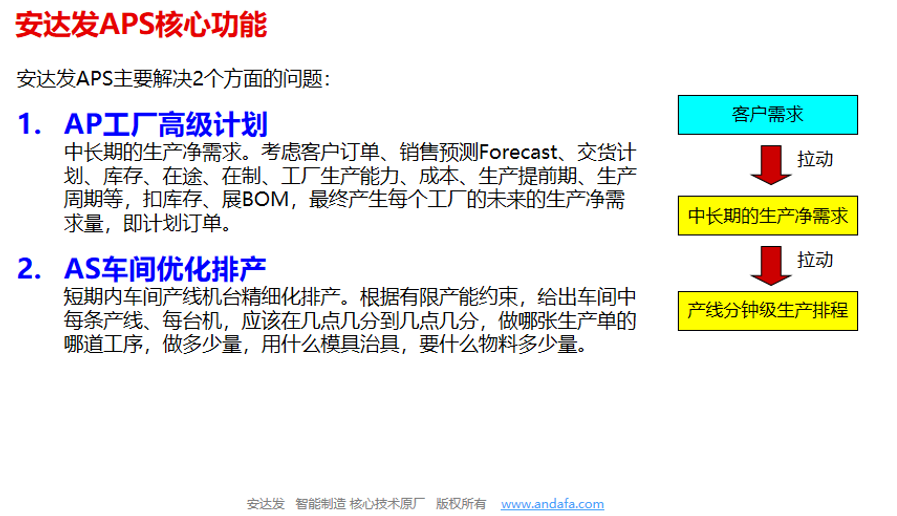
配方管理:前面提到APS系统可根据产品的BOM推出原料的需求量,润滑油企业与其他制造业不同的是,其产品调合配方拥有几种不同的方案,且基础油和添加剂的价格每月波动,按照以往的方式需要采购员将每种原料的价格导出,使用 EXCEL格表格进行一一比对,工序复杂且涉及范围较窄。
通过APS系统与ERP系统的交互,可以获取基础油和添加剂当月的价格,在原料充足的情况下对多个配方方案进行价格比对,大幅降低企业的生产成本。
看板管理:在APS系统的生产过程执行完成后,生产管理 人员需要以日、月为维度对生产情况进行复盘,此时需要 APS系统采集各功能模块的数据进行汇总,形成可视化看板。看板的主要内容如图 4 所示,主要囊括当日生产情况、月度生产情况、影响生产因素、各生产装置的OEE等方面。通过可视化看板的内容 ,生产管理人员可对生产薄弱的环节进行有针对性的改进提升,同时可以结合不同类型产品的生产情况对销售部门给出促销意见。
润滑油企业可通过搭建APS系统与MES、ERP、 UMS系统的接口,取得生产、库存、质量方面的有关 数据,减少线下报表的数量和“人机交互”的频次。完成生产订单的闭环管理,大幅提高生产计划的及 时性和准确性。此外,安达发APS系统可以结合订单优先级去分配企业内部有限的资源,不仅提高企业生产的信息化及智能化管理水平,还有效节约了生产成本,实现企业效益的最大化。