APS生产计划排产在注塑行业的应用
注塑行业越来越广泛,我们日常生活中小到孩子的玩具,大至汽车,坦克等,然而不管哪个行业多少都会存在一些难点,注塑是一种工业产品生产造型的方法。产品通常使用橡胶注塑和塑料注塑。注塑还可分注塑成型模压法和压铸法。
注射成型机(简称注射机或注塑机)是将热塑性塑料或热固性料利用塑料成型模具制成各种形状的塑料制品的主要成型设备,注射成型是通过注塑机和模具来实现的。
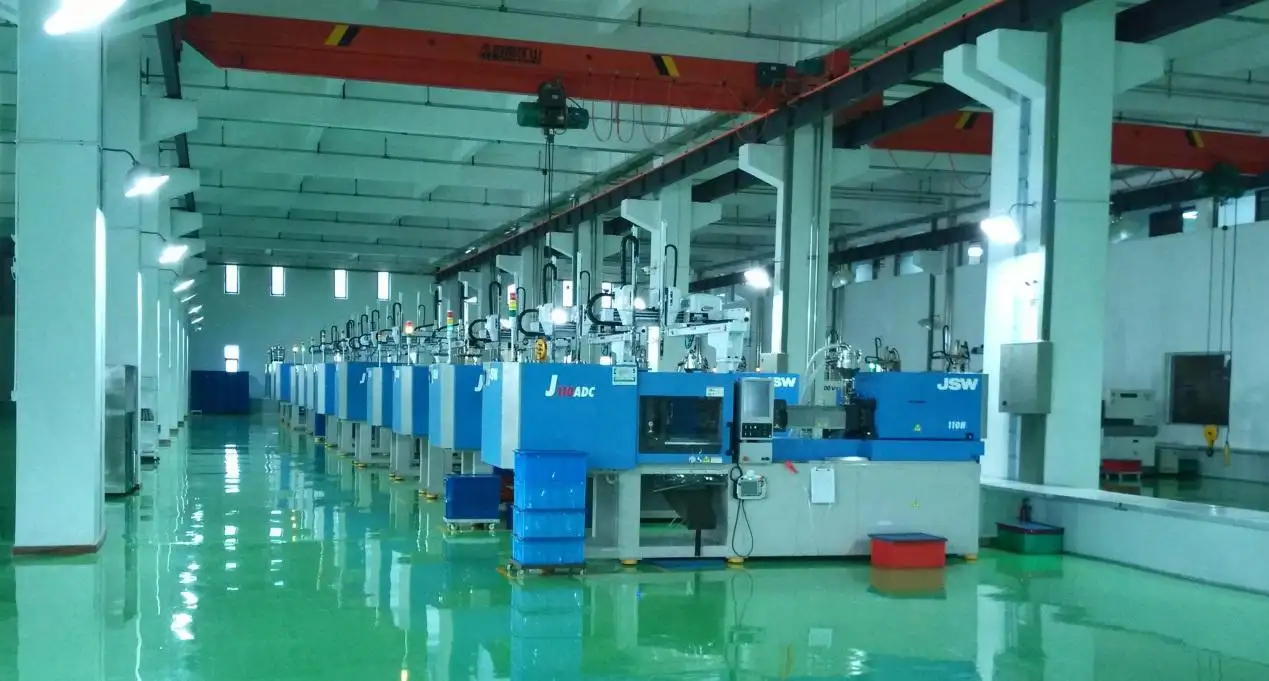
注塑行业是典型的离散型制造行业,具有多品种、小批量的特征,行业具有一下特色:
- 产品规格型号多,需要考虑的因素多;
- 排程需要机台和模具共同约束,缺一不可;
- 须考虑合并优化,包括产品、模具、塑化区温度、材质、颜色等排产优化。共模产品连续生产,减少模具更换,再由材质、颜色决定生产顺序,减少洗机时间,避免注塑机频繁升温、降温,保障生产工艺的连续性。
目前,大多数的注塑企业都有以下几大难点:
- 注塑物料的采购周期短,注塑产品的交货期压力大注塑企业客户的需求变更和市场变化较快,产品更新换代周期缩短,交货期压力大;
- 由于采购物料以大宗物料为主,对于供货的持续能力要求较高;
- 插单改单现象多,排程以及改动非常困难 注塑企业因客户的需求,经常会改变生产计划以满足客户的要求,主要表现在日期变更,颜色变更,数量变更以及新单记入等。在实际生产中,因生产赶不上进度等原因,也会进行改单的情况。因为单和单之间的相互影响,所以排程以及改动非常困难;
- 机台直接决定可生产能力,排程直接到机台 注塑机的压力级别可直接决定可生产能力,配置不同的模具对应不同的产品,但由于需要优化注塑机生产,情况比较复杂,所以需要排程直接确定哪个机台;
- BOM配置结构复杂,管理难度较大 注塑产品的BOM构架比较复杂,可配置类的物料较多,例如:颜色、材质等;如果采用传统的BOM管理经常会造成混乱,出错机率增大;
- 一次可产出多个产品,偶尔有塞模情况 某些情况下,一次注塑可产出多个产品,一般分主产品和副产品,BOM中也需要设定。生产过程中偶尔有塞模的情况;
- 注塑产品制造现场管理复杂,难以准确跟踪在注塑产品的生产车间设备较多,每道工序差别较大,一方面要对物料进行加工,另一方面又要对回收料进行粉碎和管控,管理较为复杂,对于生产进度和过程管控比较困难;
- 设备和模具的管理要求较为严格,对于模具的寿命、维修、维护等都有较高的技术要求;部分注塑企业自行设计和生产模具,对于模具制造管理有较多的管理需求;
- 注塑后加工工序的管理:注塑后加工一般有丝印(移印)、喷油、烫金、超片、收缩等,虽一般非瓶颈工序,但也和注塑生产紧密相关,也需要进行管理和排程。
APS生产计划排产可以将企业的生产管理标准化、规范化,实现多种有限资源的约束,让生产计划更加智能化。
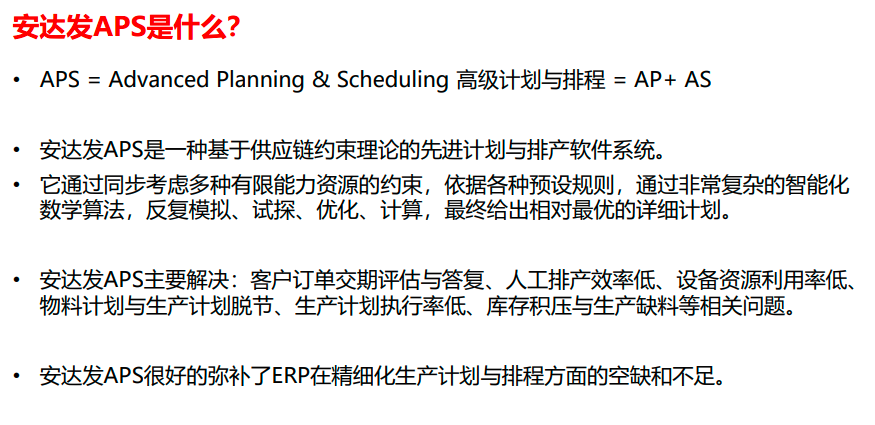
APS高级排程主要解决的问题方向:
一.将客户长期需求计划分解为日周月生产计划:
- 未来每天、每周、每月内,分别要完成什么产品,多少量;
- 一般精确到3+9+2,即:3周内的每日需求计划,9周内的每周需求计划;
- 2个月内的每月需求计划。
二.短期内车间产线机台精细化排产:
自动排产软件生产车间中,每条产线、每台机,应该在几点几分到几点几分,先做哪张生产单,先做多少量,用什么模具治具,要用什么物料,用多少量。
APS计划排产可以根据排程结果拉动人力、物料、设备等需求计划,提高设备利用率,充分利用设备产能,采用JIT式采购与供应商送货,减少长期采购资金的占用及物料库存积压,提高仓位利用率,降低库存成本,减少停机换产损失,显着减少计划人员的工作量。
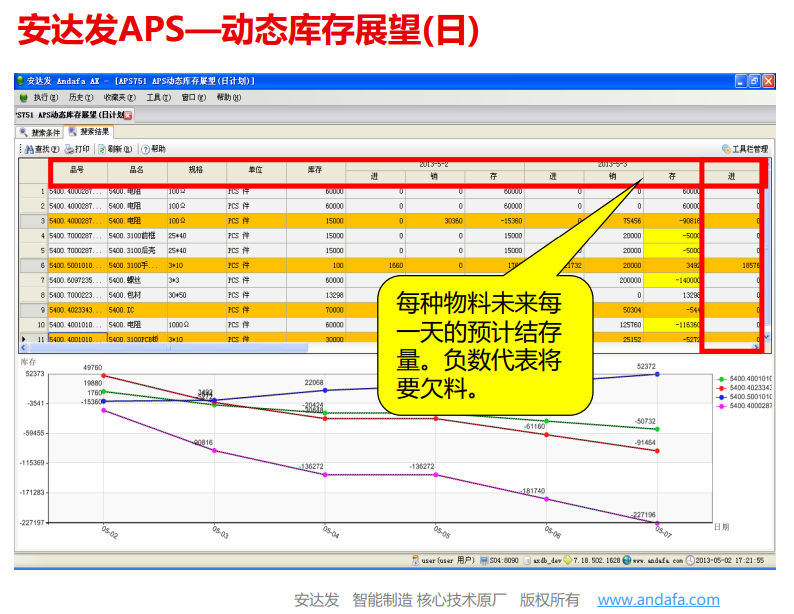
APS排产通过预先设定好相关基本资料与约束规则,自动考虑各种影响生产计划的因素,应用各类预设规则,最后给出最优化的计划方案,当订单、机台、工具、材料、上下班时间等任何影响生产计划的因素变化后,执行“一键式排程计算”,系统即可生成生产详细排程,也可选择不同的排产方案,可以实现不同的排程效果,也是设置无人值守的自动定时排程。
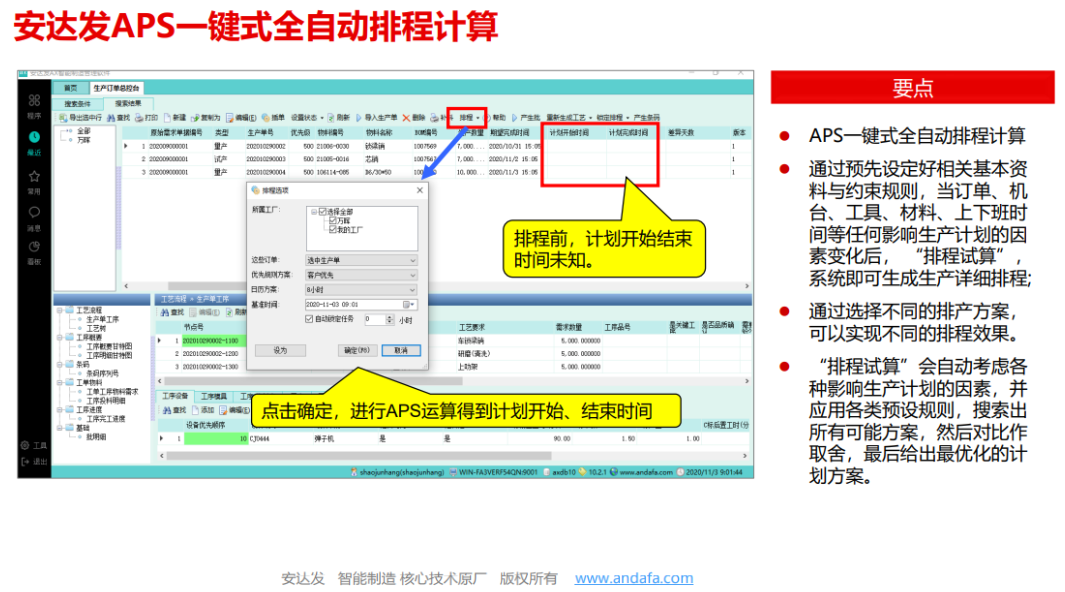
APS生产计划排产能够实现注塑企业的智能化排产,解决企业在生产排产上的难题,保证交期的最大准时化,降低运营车成本,提升企业的管理效益。