APS自动排产在企业生产中的应用:生产整体优化
APS系统,又名高级计划与排程(Advanced Planning and Scheduling),企业管理软件。是对所有资源具有同步的,实时的,具有约束能力的,模拟能力,不论是物料,机器设备,人员,供应,客户需求,运输等影响计划因素。不论是长期的或短期的计划具有优化,对比,可执行性。
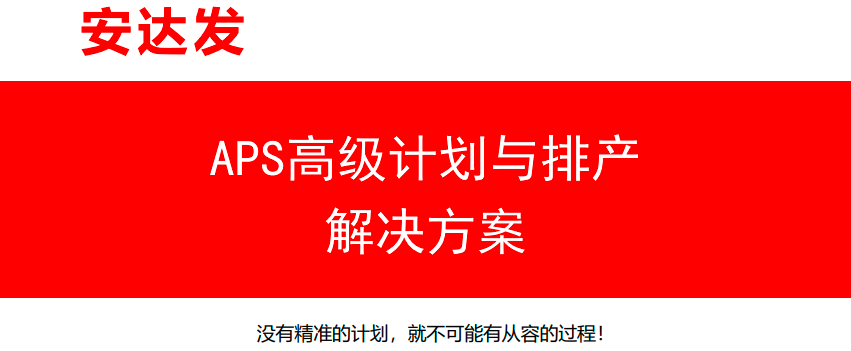
APS自动排产主要解决的问题:
- 客户需求经常变化,计划总是跟不上变化,插单的情况多,生产计划的调整及调度比较困难;
- 生产出现状况,交货期经常发生延误,无法正确回答客户的交货期;
- 无法准确预测未来机台产能负荷,无法均衡分配产能;
- 经常发生原材料、零部件的备货不足;
- 半成品、原材料的库存水平非常高;
- 计划人员过多,工作协调性差,效率低而且容易造成经费的浪费。
APS自动排产从“交期、成本、管理”这3个方面显着提升您企业的竞争力,确保交期、降低成本,提升管理!
APS自动排产是通过同步考虑多种有限能力资源的约束,依据各种预设规则,针对解决:客户订单交期评估与答复、人工排产效率低、设备资源利用率低、物料计划与生产计划脱节、生产计划执行率低、库存积压与生产缺料等相关问题,依靠严谨的数据及逻辑运算,终给出相对最优的详细计划的一种基于供应链约束理论的先进计划与排产软件系统。
APS排产通过预先设定好相关基本资料与约束规则,自动考虑各种影响生产计划的因素,应用各类预设规则,最后给出最优化的计划方案,当订单、机台、工具、材料、上下班时间等任何影响生产计划的因素变化后,执行“一键式排程计算”,系统即可生成生产详细排程,也可选择不同的排产方案,可以实现不同的排程效果,也是设置无人值守的自动定时排程。
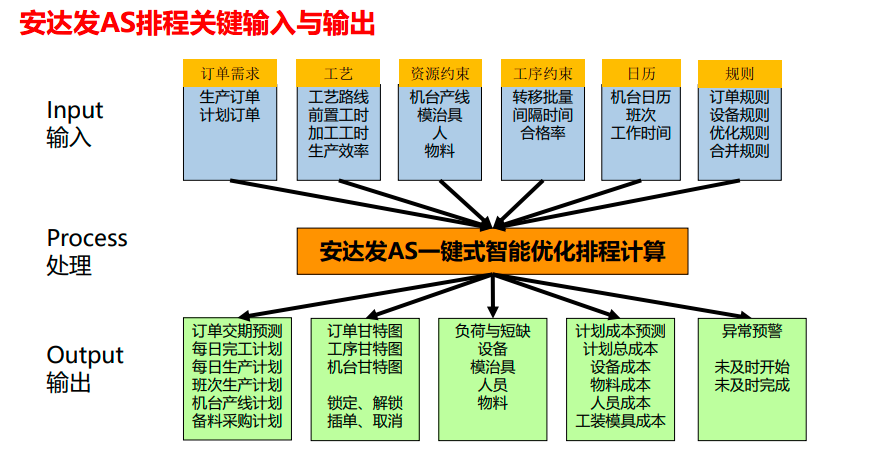
APS生产排程通过对工艺流程基础数据与资源约束,对每个工序详细设置其优化规则,进行短期排程结果的优化,将所有待排程订单按紧急程度分为3大类:特急、一般、不急,并针对每种紧急程度分别设置具体的排序选择规则,提供多种手工调整的方法,可灵活的对排程结果做可视化的拖动调整,从而实现了个别个性需求的灵活处理,从而实现工艺的基本资源约束,达到大范围急单先做的效果,显著减少换产带来的工时和物料的损失。
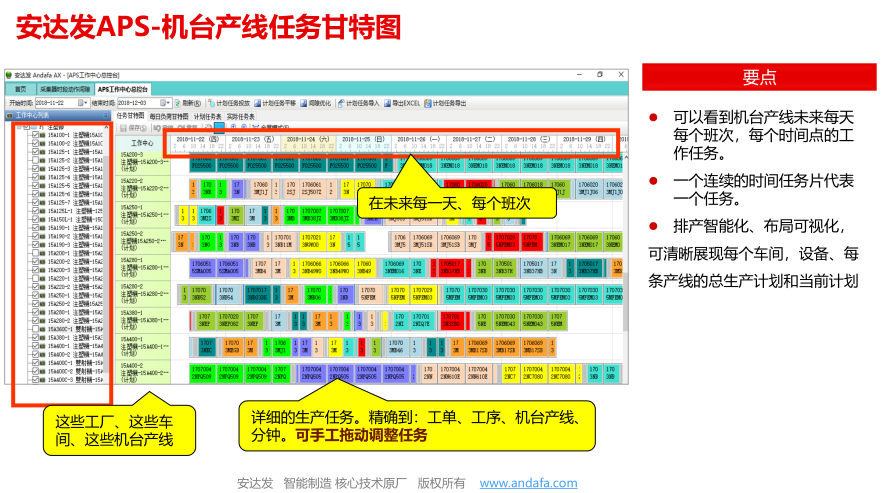
APS自动排产依靠严谨的数据及逻辑运算,短时间内分解长期计划到日计划(短期内车间产线机台精细化排产),可以实现多任务工序的前后联动,并自动扣减完工数和库存,并自动产生多种直观化报表。
APS自动排产可以根据排程结果拉动人力、物料、设备等需求计划,提高设备利用率,充分利用设备产能,采用JIT式采购与供应商送货,减少长期采购资金的占用及物料库存积压,提高仓位利用率,降低库存成本,减少停机换产损失,显着减少计划人员的工作量。
APS自动排产能够实现生产资源的约束,对企业生产进行整体的优化,让生产管理标准化、系统化,减少人为疏忽与误差导致的一系列后果,使得生产有序,客户满意度提升。