一文读懂APS与MES!
在工业4.0理论,APS、MES、PCS必须嵌入式融合,通过行业经验知识,建立合适的计划与排产模型,对所需的实时数据,动态智能决策。这应该是工业大数据的关键应用。
1.APS与MES概论:
APS高级计划系统(AdvancedPlanning System)或高级计划与排程(AdvancedPlanning and Scheduling),分供应链级的APS和工厂级的APS。供应链级的APS侧重于SCP(Supply Chain Planning)供应链计划的优化,包括网络配置计划、需求计划、库存计划、多工厂计划、供应计划等的优化。工厂级的APS侧重于交期承诺、计划与排产、加工顺序调度、物料准时配送等的优化。
APS功能分高级计划AP(AdvancedPlanning)与高级排程AS(Advanced Scheduling)。每个APS软件供应商在AP和AS各有擅长,但其共同的特点是:1、各种资源约束的优化算法。2、基于常驻内存计算,计算速度快。3、可模拟What if.
APS的优化算法主要分四代:第一代:基于约束理论的有限产能算法。第二代:基于优先级等规则的算法、线性规划、基于启发式规则的算法、专家系统。第三代:智能算法、遗传算法、模拟退火算法、蚁群/粒子群算法、神经网络。第四代:智能算法融合人工智能动态调整算法,以智能算法进行静态排程,以多Agent代理协商进行动态调整。
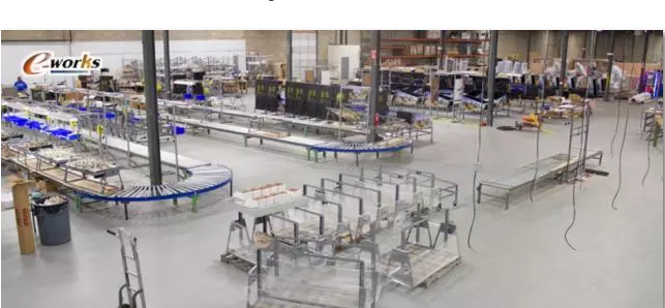
不同的APS软件供应商选用不同的优化算法搭建自己的高级计划与排程系统软件,需要根据不同行业特点解决不同的场景问题来决定采用哪种优化算法。
APS为离散行业解决多工序、多资源的优化调度问题。为流程行业解决顺序优化问题。为流程和离散的混合模型同时解决顺序和调度的优化问题。对项目管理与项目制造解决关键链和成本时间最小化问题。
MES(Manufacture Executive System)制造执行系统,早期用于SFC(Shop FloorControl )车间控制,管理工作中心WC(Work Center) 并下达派工单,主要靠手工汇报进度、工时、损耗。随着制造精益化,制造数字化,形成了MES制造执行系统,它包含了11个模块:
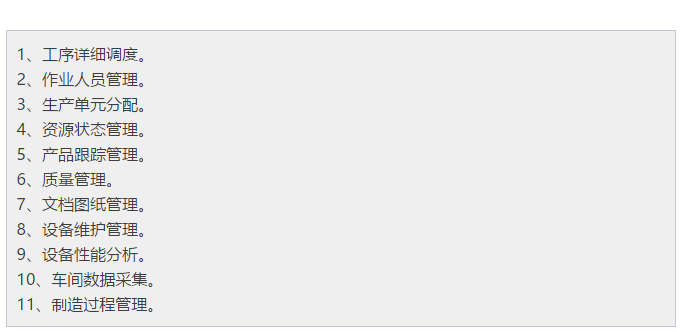
主要管理车间的人机料法环,是精益生产的数字化系统,必须融入TPS(Toyota Production System)丰田生产系统和(Lean thinking)精益思想的MES。
现在,MES仍不断进化,包含工厂级的APS的计划与排程和PCS工控的设备过程控制。PCS(Process Control System)过程控制与监督实现人、机、物互联。
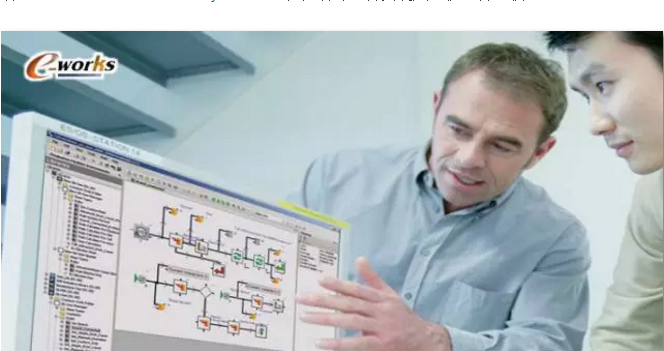
MES是数字化工厂的核心,将前端产品设计、工艺定义阶段的产品数据管理与后端制造阶段的生产数据管理融合,实现产品设计、生产过程、维修服务闭环协同全生命周期管理。
MES是数字化工厂的核心,将前端产品设计、工艺定义阶段的产品数据管理与后端制造阶段的生产数据管理融合,实现产品设计、生产过程、维修服务闭环协同全生命周期管理。
APS和MES在AS排产功能是重叠的。不过,现在的趋势是APS和MES、PCS融为一体,实现四个闭环:
1、需求预测和订单承诺闭环。2、计划与排产闭环。3、排产与执行闭环。4、订单承诺与订单履约发货闭环。形成系统自治,自反馈、自决策。2.APS起源:
APS系统最初起源于制造商对于更好的时间安排和优化计划工具的需求。制造商几乎都需要更实时的,更灵活的生产计划系统。然而,在第一个APS系统发布以后,商务运行的模式开始发生了变化。所有制造商都意识到快速,积极响应客户需求的重要性。所以,最初APS系统的设计是用约束和列队模式的简单理论来解决瓶颈问题、工序顺序问题。
然而,现在,却发生了改变。新的APS系统则能较好的处理业务级的优化顺序和及时修正反馈,以及物料与绩效需求的问题。同时也能在供应链的多地点之间提供精确的,实时的承诺计划。
从20世纪40年代以来,用数学方法进行精确计算来安排生产计划,就一直是一个传统的研究课题。线性规划作为管理科学的基础,在管理理论的教科书中比比皆是。数十年来,学院派的学者对这个课题的研究乐此不疲。但是现实世界太复杂,理论与实际存在较大的距离,即便使用大型计算机,也未取得可行的应用。随着MRP方法的诞生,生产计划管理领域就形成了两种方法或两种计划思想的发展道路,存在着并行的两种编制生产计划哲理:MRP法和数学解析方法。
在20世纪80年代中期,改进的MRP,缩短了计划运行时间,开发了一种快速MRP的模拟技术。这种方法将复杂的生产作业模拟在独立计算机上,部分采用以常驻内存方式进行批处理运算,脱离了当时占业务计算支配地位的主机,使制造企业完成生产计划排程只用几小时而不是当时所公认的20多个小时。虽然当时的尝试并没有考虑计划的约束条件,但它已经成为一种新的计划与排程方法的开端。
著名的OPT发明人以色列的科学家高德拉特(Eli Goldratt)对 APS的发展有显著的功绩。优化生产技术(OPT)本身就是一种根据能力的瓶颈实行计划的哲理,后来他又继续发展成为约束理论TOC(Theory of Constraints),开始在离散制造业的优化排序中应用,出现了第一批的APS系统公司和基于常驻内存运行的交互式的APS产品。
1984年AT&T推出的 Karmarkar’s 算法,成为线性规划突破性进展,之后几乎被所有现代LP解决方案所采用。其后,新的APS计划与排程系统开发商,他们其中许多人具有数学或运筹学高级学位,花费多年的心血,将线性规划等优化方法适用化,实用化。
在新一代计算机技术的支持下,创造出几乎能在瞬间生成的优化计划程序,使理论化的数学解析计划方法达到了实用程度。这些新的软件包被称为APS引擎(AdvancedPlanning and Scheduling engines)。在MRP的鼎盛时期,先进的计划解决方案APS引擎的成熟,使生产计划方法的交替不可避免的发生了。因此,ERP也出现了继续完善和功能扩充以及改变ERP的功能和性质这两种发展趋势。
基于约束的高级计划和排程技术的是真正供应链优化的重要引擎,她给错综复杂的供应链丛林中的企业以敏捷的身躯,来快速反应与适应激烈竞争切变化多端的市场。实际上有多种需求导致APS的产生。其原因如下:
- ERP的计划系统MRP/CRP的缺陷无法应对业务的发展。直到现在,对许多使用业务系统的人们来说高级计划APS还都是新的内容。
- APS的内部开发已经完成,技术已走向成熟,出现很多的供应商和产品的现象。
- 许多咨询公司还没有涉足此领域,直到较好的产品和供应商出现。
- 人们对APS的定义来源于较广的工业领域。APS在不同的时间、不同的运用点渗透到不同的工业领域。当公司有能力管理自己的数据与业务时,实时、优化就显得更加的重要。流程行业最先使用APS技术,离散行业较后才使用。
- 许多用相似的方案的供应商已经很积极的声明自己是APS供应商。
- 对APS技术的贡献有APICS美国生产与库存控制协会、人工智能、计算机科学、决策支持系统、工业工程、物流、管理科学、运筹学和生产运作管理。每一个领域都有自己的术语。也导致了一些混乱。(甚至”计划”与”排程”都没有标准的意义),这也造就了创造新工具的机会。
APS已经从企业内部持续改善的优化工具到满足公司间协作的供应链新技术的进化。这个论题是John Layden,在他的《排程逻辑的进化》的文章描述的,让我们继续这个进化,看看有谁在此领域活跃了近二十多年。
3.计算机出现之前的APS。
在计算机之前,一些关键的概念已经形成了。一个是甘特图,它让人们看到可视的计划并可以交互的更新。这个简朴的概念一直延续到今天,我们用有颜色的橡皮带、块、钉子和粉笔在墙上,纸作标识。用数学建模的方式来解决计划问题的想法出现在至少在1940年。美国和前苏联让人们手工应用这一新的优化技术,它叫线性规划,运用它来解决与战争有关的后勤问题。
4.1950-1960初,计算机已出现。
APS的进化已经和计算机的进步紧密相连了,在1950末或1960年初,许多大公司开始租赁计算机计算和购得大型计算机。计算机被用于研究计划问题的一部分,如优化几个关键的物料和能力的平衡,基于产品的需求与能力约束,或者找出批量产品的最低成本的配方。他们一般都使用线性规划的算法,其数学模型就象现在的小型的电子表应用程序(40-60个方程式和60-100个决策变量)。在此其间,有两个公司首先提供对计划的优化工具,他们是在1957成立的Bonner and Moore公司和1962年成立的Haverly Systems 公司。优化的处理可以避免混乱,优化技术的严格实施是一个较好的解决方案或方法,保证找到对问题的”最好”的答案且智能的知道何时发生,多长时间发生。
今天,我们使用优化技术常常是用于一个较简单的寻找提高的方法或方案且不能保证找到最好的方案。简单的寻找提高的技术叫启发式算法,它们经常用于时间的限制或容限.(在10分钟,找到最好的答案)。线性规划较适合严格的优化约束和识别约束,经常是对一个问题用于经济上如成本和收入的约束来决定”最好”的方案。
5.1960中期-1970初 计算机应用程序的进步。
随着计算机的进步,人们有能力可以考虑更复杂的计划问题。先进的技术的工具可以考虑整个制造工厂和设置在最小化成本的运作且最大化利润。一些公司结合计算机程序对生产设备来优化他们的产品配方。人们也开始研究供应链分销问题,如公司EXXON开发程序来集成库存、采购、制造、分销管理。
从1960初的几百个决策变量到1970的几千个变量,到1970年的后期的上万个变量,线性规划的这种技术也扩展到解决更困难的问题。如生产能力的决定,生产品种和生产线的选择和对分销中心的选址等。这些应用最早是出现在流程行业的计划层,许多大的化工公司如Amoco, Chevron, Exxon, Marathon和Shell都积极采购主机系统的计算机,部署到他们的制造工厂里,这些公司还采取了数据采集与集成数据的方法。由于业务的需求推动,优化技术较好的满足他们的许多流程和分销网络的特点。
许多公司自己在大型机环境下开发自己的工具,开发线性规划的程序。也可以从几个供应商购买到。如IBM的MPS(后称MPSX),有些公司却使用现成的程序开发语言如Assembler, Cobol,FORTRAN,和PL/1是常用的开发语言。这些程序是以批处理的模式运行。
计算机已成为解决排程问题的工具,模拟也被用于制造和分销设施的设计。模拟工具还开发成计算程序, 按照能力和物料的消耗、顺序活动、计算批量可以得到排程的结果。可以对特别的排程问题进行开发的,且这些程序界面可以为用户交互使用。
基于排程工具的模拟开始出现在1970年,Pritsker是一较早的供应商,另外一早期的产品是IBM的CPPS.主要是些化工公司。在1970年就积极使用了计划工具,其他行业也在积极使用计划和排程程序。
1980年初,轮胎制造商Kelly Springfield ,PhilipMorris 已经使用了APS计划和排程程序,造纸公司如St Regis和国际造纸也实施和运用了APS工具。
6.1980年,商业媒体发现了APS。
约束理论的发明者高特拉德(1983年9月5日财富杂志人物)领导的创新产出公司(Creative Output)的产品OPT,以批处理的模式,应用一系列的消除瓶颈的算法获得了许多离散制造业的客户。创新公司在和M&M/Mars公司的法律争端之后,从市场很快的退出。而高特拉德扩展了TOC(约束理论)的哲学,他本人却以出版和制造导师为职业。当时和创新公司的同类的I2公司仍然活跃在APS领域。
财富杂志的文章还提到Numetrix决策科学公司。它以后又分拆为Numetrix公司和Chesapeake决策科学公司。这两个早期的APS供应商具有交互的产品和提供基于内寸计算技术。(Numetrix被ERP厂商JDE收购,JDE被Oracle收购)。
在APS文章经常出现学术论坛和使用APS方案的期间,产品介绍开始出现在“商业周刊”,“Chicago Tribune”,“New York Times”,“Wall Streetjournal”, “Washington post”。
媒体关注的中心是在1984年,由年轻的AT&T的研究者名为Narendra Karmarkar 开发的算法,这个新技术解决了线性规划的问题,是AT&T作为“真正的突破”和“设计解决了以前未解决的问题”。AT&T把这个算法绑定他们的计算机,价格近9百万美元。
在1980年中期,许多大的化工公司认识到可用改善制造流程来阻止下降的利润,就开始检查他们供应链的活动。BASF,DOW,Du Pont和Rohm和Haas都开始积极使用计划和排程的工具,他们使用自己开发的产品和工具或自己修改过的APS产品。目的是想要管理真正的整个供应链而不是某一局部的方案如制造或分销。
许多MRPII的供应商,为了满足市场需求也进入流程行业。有些公司却延迟开发APS工具或使用APS工具,他们决定用MRP,CRP来满足他们计划和排程的需要。但是,在1990年初,许多大的化工公司已经选择了APS的供应商。许多大的航空公司也实施了复杂的计划和排程系统,美国航空集团也为其它航空公司建立这些高级计划排程系统。
1980年后期,我们也看到了人工智能,专家系统的出现,许多公司把人工智能运用到计划排版程系统,客户期望的难题就此解决。DuPont和IBM积极结合人工智能AI和存在的技术开发程序,IBM也开发了一个派工系统。
Du Pont用Chesapeake决策科学公司的MIMI优化,把模拟启发的产品里加入了专家系统。专家系统用它的数据验证、启发式的协作、方案解释的能力,为计划排程的制定起到有效的作用。
实时的专家系统产品如G2在此时也出现了。人工智能AI世界同时也对APS的技术作出了贡献如基于规划的约束和基因算法。用人工智能AI完全达到期望的要求,可能令人失望。
1980年后期,也出现了图形用户界面,有些供应商试图结合个人计算机来增加它的图形运用能力, 图形用户界面成为标准的预测、计划、排程工具的一部分。这个技术革命,巨大的影响了APS的市场化。
7.1990年,APS市场繁荣和产品增值。
在1990年初,消费品公司(CPG)开始联系APS系统,虽然也有一些早期采用者。在此市场阶段,这个行业作为一个整体应用APS技术是很慢的。一些已经有能力实施相对简单的制造排程的公司发现他们需要更复杂的系统,可以处理包括SKU数量,分销网络的地点的选择。
许多公司也发现相似的问题,就是他们的预测能力,尤其是在SKU的数量的管理上, 简单的预测工具却阻碍了预测的准确性,他们需要集成供应链的多地点的详细的需求,来为了供应链运作决策。
1990年初,SQL的引进,允许APS工具和关系型数据库更动态的互动。计算机能力的增强和成本的降低,导致新的方案的出现。同时也发现问题的复杂性,导致基因算法出现。人们开始使用反复模拟,想要建立更好的方案。但是,随着开发的工具处理百万的决策变量,对计算机和应用程序是一大挑战。
1990年,APS的供应商已经覆盖到更广的工业领域,如I2、Fastman进入电子装配、金属品制造等离散制造领域。I2的市场导向和销售战略,戏剧性的提高APS的空间。而这以前APS都是一直技术导向的市场,由于I2、Manugistics等的公司的影响,引起了大咨询公司的注意。他们开始分配资源给这些产品作服务。但是,APS对大的咨询公司而言有两个挑战。一个是它需要较深的应用专家,而不是集中在IT的应用上。二是固定的、标准项目实施方法对APS项目不太有效,该领域的专家仍然需要决定如何更有效的实施APS。
1990年中期,许多供应商转向微软技术的视窗环境下的用户界面,除了提供更直观的用户界面,报告能力而且使APS应用程序的环境转向低成本的、性能戏剧性的提高的计算机。1990年中期,也看到了APS运用到部分的半导体公司。这些公司在改变产品技术方面有着极大的进取心,使产品具有极短的生命周期,这就对APS来说是一大挑战,特别是在计划和排程。
使用APS技术的公司有Harris半导体公司、IBM公司、Intel公司、Texas 仪器公司,用APS技术解决自己业务的复杂问题.
最后,在1990年的中期,APS还吸引了大多数ERP供应商的注意,随着APS市场的快速成长,产生了ERP供应商的新一轮的收购APS公司或自己内部开发APS。许多专家认为APS必须嵌入ERP系统。
总之,从二次大战以后,我们在生产管理上的生产计划上开发了很多类型的生产计划系统,最早的是用EOQ经济订货点系统,2-Bin双箱系统,LP线性规划系统。后来在美国,由于物料资源较为丰富,在生产管理上,管理者主要集中考虑人工的效率,所以产生了基于无限约束的MRP物料需求计划,同时在资源比较匮乏的日本,研究开发出了精益JIT看板拉式系统,主要集中考虑减少物料的浪费。同时,在以色列,主要研究关键资源的能力效率,所以产生了TOC约束理论,以提高瓶颈资源的效率来整体提高企业效率。在一些项目管理时间较长的制造环境下如(造船),美国海军设计出了PERT计划评审技术/CPM关键路径法。随着管理的需要,MRP系统与财务的结合就产生MRPII制造资源计划系统来优化企业制造资源。现在管理资源的领域已扩展到工程、人力资源、供应商、分销的ERP企业资源计划系统以整合规划企业资源。
不幸的是,以上的系统都没有较好的解决企业效率的基本问题:约束。FCS有限能力计划系统利用并扩展TOC的原理,全面进行多重资源约束的优化计划。但是,仅仅能力约束还是不够的,还要考虑物料的约束、需求的约束、供应商资源约束、运输资源的约束、分销资源的约束、财务资金的约束。即产生了APS高级计划排程系统。同时把JIT和TOC的优势结合在一起,又产生了DFM需求流制造系统。现在,企业的竞争就是供应链的竞争,整合企业上游下游的供应链,使之形成供应链联盟,就需要用到SCM供应链协作的SCP供应链计划。
8.APS发展趋势与我国APS应用展望。
二十一世纪是信息时代,经济全球化步伐日益加快。作为代表当今先进管理思想的高级计划排程系统,APS的发展呈现以下趋势:
- 与供应链管理更加紧密结合。小巧灵活的APS系统将为中小企业的计划优化服务。
- 集成化与分散化。APS则成为各种计划技术与方法的系统融合,体现了计划思想的高度集成。然而,由于现实问题的复杂性,如不同的行业与产品特点、不同的企业规模等,对一些企业来说,采用庞大完整的APS系统并不是最佳选择。而结合行业与产品特点、各具特色的先进计划系统同样是APS的发展趋势。
- 与多品种小批量订单制造和项目制造结合。由于消费者个性化需求的日益增长,产品大量生产的时代即将过去,多品种小批量、个性化时代已经到来,APS必然是企业整体的计划管理系统。
尽管APS具有强大的功能,非常适合于供应链整体计划问题的解决,但在我国企业管理实际中,APS应用仍然存在很多需要解决的问题:
- 外部应用环境。APS功能的发挥主要在供应链管理上,而我国企业的供应链管理还停留在非常初级的阶段,企业对于供应链竞争的意识还很模糊,因此,APS难以找到真正的用武之地。
- APS需要全社会企业间的网络通讯基础设施的支撑,而我国的网络基础设施建设还不够完善,企业网络应用水平还很低,这些都阻碍了APS的应用。
- 企业内部信息化基础数据、流程、计划体系薄弱。APS的运行需要有ERP、MES、PLM等系统提供的数据支持。
- APS系统的平台化,通用化的APS产品很难面面俱到解决各行业的问题,而且越是考虑的行业多,越会导致系统参数很多,使用难度加大,系统友好性变差,计算效率降低,最终实施效果变差。APS软件一定要是平台化、可快速客制化修改。生产管理本来就复杂多变,精细化的生产就更是复杂多变。如果不能快速客制化修改,则很难解决好客户的实际问题。
智能制造与工业4.0下的APS。
作为智能制造的源头,智能计划排产是工业4.0的核心技术之一,只有实现计划排产的精准化与最优化,才能实现整个生产过程的智能化。
在实现CPS之前,应用APS系统,一方面提高了实际生产与进行计划的信息技术系统的价值,另一方面也提高了生产管理人员和所使用的信息系统的共同生产力。
APS系统必须应用工业大数据技术,制造业面对多品种小批量的生产模式,数据的精细化、自动及时方便的采集(MES/DCS)及多变性导致数据剧烈增大,再加上十几年的信息化的历史数据,对于需要快速响应的APS来说,是一个巨大的挑战。
在工业4.0理论,APS、MES、PCS必须嵌入式融合,通过行业经验知识,建立合适的计划与排产模型,对所需的实时数据,动态智能决策。这应该是工业大数据的关键应用。
APS系统也正朝着分布式计算(智能代理技术等)和自主认知计算(人工智能、机器学习等)发展,形成工厂级的CPS(CyberPhysical Systems)信息物理系统,其特点分布式计算、自主智能决策。
数字化工厂平台是CPS平台的基础,要实现分布与自主(CPS的关键特征),还有很长路要走。也就是说从计算智能APS到认知智能CPS,需要计算架构的颠覆!
APS高级计划排程系统是20世纪后50年发展起来的革命性管理技术,融合了现代新技术与先进的管理思想,是计算机技术与管理思想的结晶。APS弥补了ERP在计划上的缺陷,成为今天计划的核心。但是,由于信息基础设施落后、企业信息化程度很低,APS系统应用在我国还有很长的路。随着我国社会信息基础设施的日益完善、企业信息化水平的逐步提高,中国制造2025的智能制造的强力推进,可以预言,未来三到五年内,APS在我国的应用将开始进入实质性阶段。