安达发|生产计划天天改?APS智能排产如何动态优化,让调度不再‘救火’!
在制造业中,最让管理者头疼的莫过于"计划赶不上变化"。订单临时调整、设备突发故障、供应链中断……任何一个意外都可能让原本周密的生产计划变成一纸空文。传统的人工排产方式往往反应迟缓,导致生产效率低下、成本飙升。
然而,随着高级计划与排程系统(APS)的普及,企业终于找到了"以变应变"的解决方案。APS的动态调整能力到底有多强?它如何让工厂在瞬息万变的市场中保持高效运转?
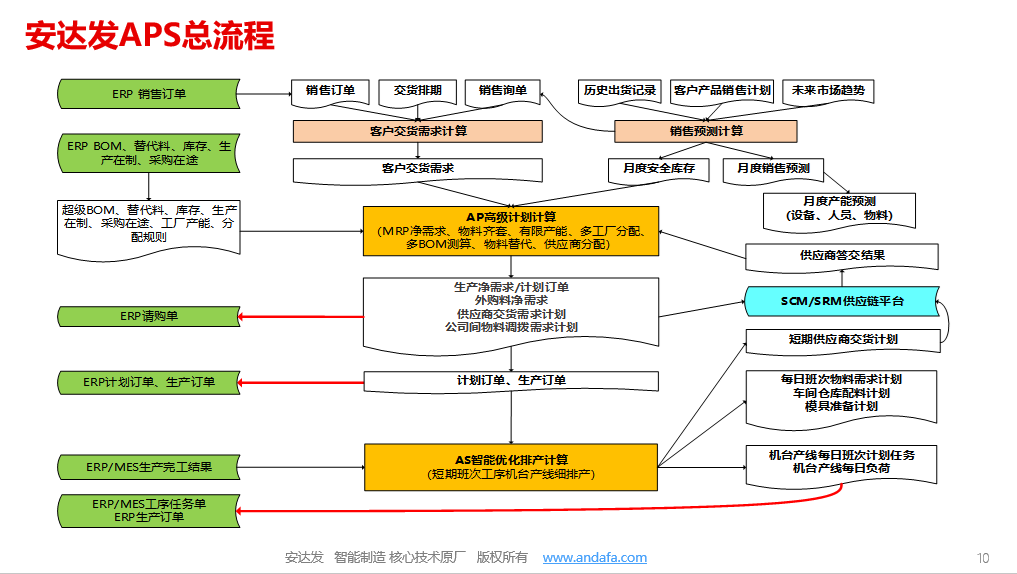
1. 传统生产计划的困境:为什么"计划赶不上变化"?
在APS智能排产出现之前,工厂的生产计划通常依赖人工经验或静态排程工具,存在几个致命缺陷:
• 反应速度慢:当订单变更或机器故障时,人工调整可能需要数小时甚至数天,导致生产停滞。
• 依赖经验决策:排产员往往凭直觉调整,难以兼顾设备利用率、交货期、库存成本等多个目标。
• 无法全局优化:传统ERP系统只能提供固定排程,无法实时响应变化,容易造成资源浪费。
例如,某家电企业曾因上游原材料延迟到货,导致整条生产线停工3天,损失超百万。类似的情况在制造业屡见不鲜,凸显了传统计划的局限性。
2. APS智能排产如何实现"以变应变"?动态调整的三大核心能力
APS系统的核心优势在于实时数据驱动+智能算法优化,能够在几秒内重新计算最优生产方案。其动态调整能力主要体现在三个方面:
(1)实时响应订单变化:从"被动调整"到"主动适应"
• 场景:客户突然加急订单,要求提前交货。
• 传统方式:人工重新排产,可能打乱原有计划,导致其他订单延误。
• APS方案:系统自动评估产能、物料库存、设备状态,在保证其他订单按时交付的前提下,智能插入紧急任务,甚至调整生产线优先级。
案例:某汽车零部件厂使用APS智能排产后,紧急订单响应时间从原来的8小时缩短至15分钟,客户满意度提升30%。

(2)自动应对设备故障:从"停机等待"到"无缝切换"
• 场景:关键机床突发故障,原定生产任务无法继续。
• 传统方式:工程师手动调整排程,可能造成生产混乱,延误交期。
• APS方案:系统实时监测设备状态,一旦检测到异常,立即重新分配任务至备用设备,并优化后续工序,确保整体进度不受影响。
案例:某电子制造企业引入APS智能排产后,设备故障导致的平均停机时间减少70%,生产效率提升18%。
(3)智能适应供应链波动:从"断料焦虑"到"动态平衡"
• 场景:某关键原材料供应商延迟交货,原生产计划无法执行。
• 传统方式:生产主管焦头烂额,临时调整排产,可能导致库存积压或产能闲置。
• APS方案:系统自动关联供应链数据,在物料短缺时优先生产库存充足的产品,或调整工艺路线(如使用替代材料),最大限度减少影响。
案例:某食品加工企业通过APS的动态物料调度功能,在原材料价格波动期节省采购成本12%,同时避免生产线断料。
3. APS智能排产动态调整的底层技术:为什么它比人工更聪明?
APS的强大适应力并非凭空而来,其背后依赖多项关键技术:
• 实时数据集成:与MES、ERP、SCM等系统无缝对接,确保排程基于最新信息。