安达发|塑胶行业如何通过APS生产计划排单软件破解生产排产难题?
在当今竞争激烈的制造业环境中,塑胶行业面临着多品种小批量生产、订单交期波动大、设备资源有限等多重挑战,传统的人工排产方式已难以满足高效、精准的生产需求。高级生产排程系统(APS)的出现,为塑胶行业提供了一套智能化解决方案,有效破解了生产排产的核心难题。本文将从行业痛点入手,探讨APS系统如何助力塑胶企业实现高效生产。
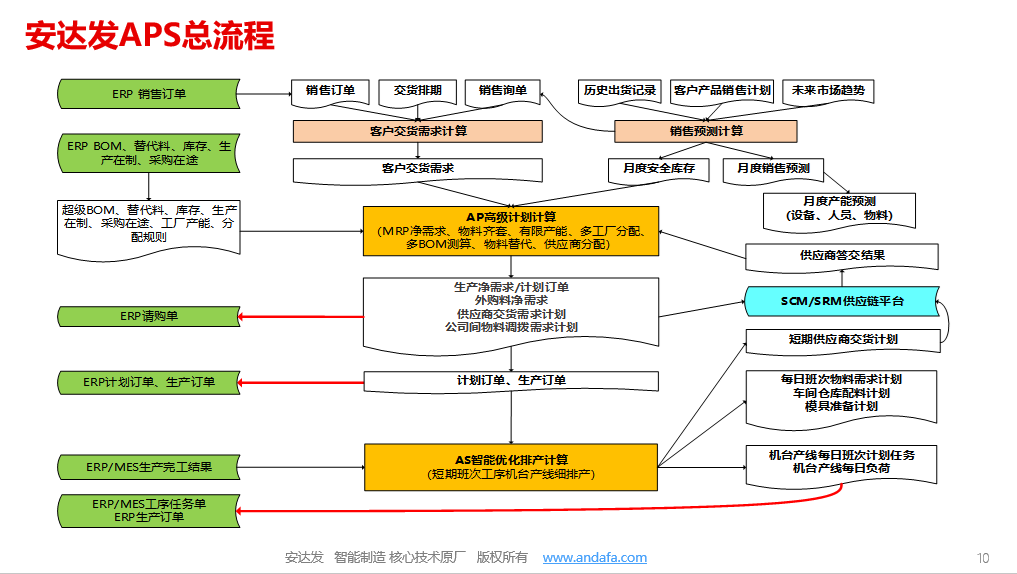
一、塑胶行业的生产排产痛点
塑胶行业的生产排产难度主要体现在以下几个方面:
1.生产复杂度高:注塑、挤出等工艺涉及模具、材料、机台参数等多维因素,同一产品可能因配方或工艺差异导致生产时间波动30%以上。例如,PVC电缆料使用双螺杆挤出机比单螺杆快40%,但能耗更高,传统依赖老师傅经验的排产方式难以量化优化。
2.订单波动频繁:客户需求多变,紧急插单或订单取消常打乱原计划,人工排产无法实时调整,导致生产混乱。
3.设备冲突与产能瓶颈:关键设备(如注塑机、密炼机)数量有限,频繁换模(如密炼机清模需2小时)直接吃掉20%的有效产能。
4.能源成本高企:橡胶塑胶行业电费占比高达8%-12%,高能耗设备排产缺乏优化,进一步加剧成本压力。
二、APS生产计划排单软件的核心解决方案
针对上述痛点,APS生产计划排单软件通过智能化算法与行业专属功能,实现了生产排程的革命性突破:
1. 智能工艺匹配与动态优化
APS生产计划排单软件内置塑胶行业“工艺知识图谱”,可自动关联配方、工艺与设备。例如,输入“高填充阻燃PVC配方”,系统会推荐“双阶挤出机+侧喂料工艺”,并预警使用单螺杆可能导致的螺杆磨损率提升50%。对于医疗级硅胶制品,系统强制关联“铂金硫化工艺+百级洁净车间”,规避合规风险。同时,系统能根据实时环境数据(如温湿度、原料批次)动态调整工艺参数,减少生产波动。
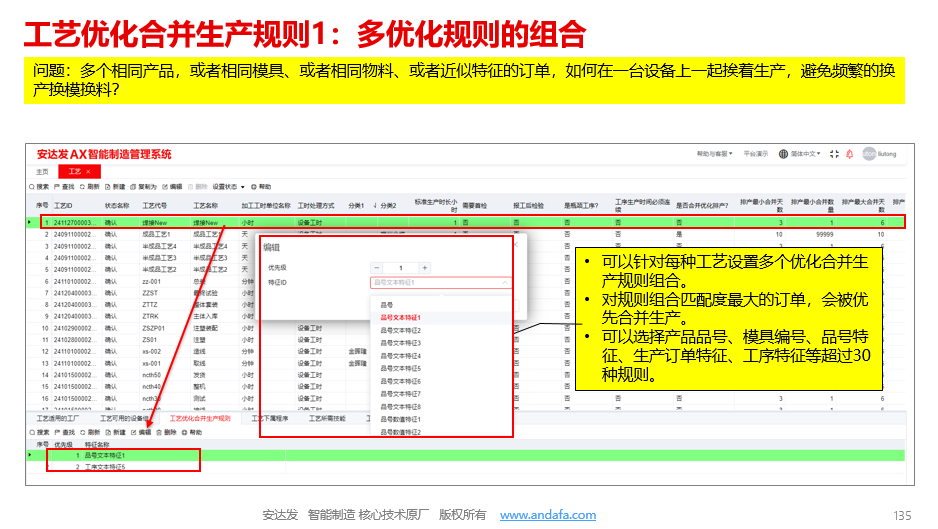
2. 设备冲突与换型优化
通过智能订单合并引擎,APS生产计划排单软件自动识别同颜色、同配方的订单,减少换模次数。例如,安达发APS可合并相同模具的生产任务,将注塑机换色时间从1.5小时压缩至最低。系统还支持“有限产能排程”,实时监控设备状态,当出现冲突时自动调整顺序或推荐替代设备。历史数据训练的AI模型可精准预测换型时间(误差≤5分钟),并自动调整后续计划,确保交付承诺。
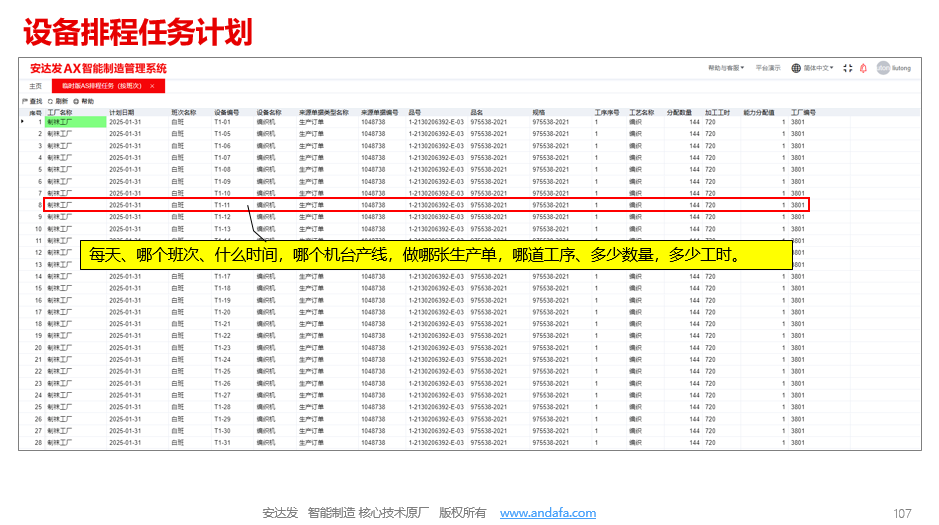
3. 插单模拟与风险管控
面对临时加急订单,APS生产计划排单软件可在3秒内模拟100+种排程方案,量化展示对其他订单的影响。例如,JVS解决方案提供“替代方案”(如部分外协、调整交期),将插单决策从“拍脑袋”变为数据驱动。对于高风险订单(如需跨车间调货),系统自动触发审批流程,避免业务部门“先斩后奏”。
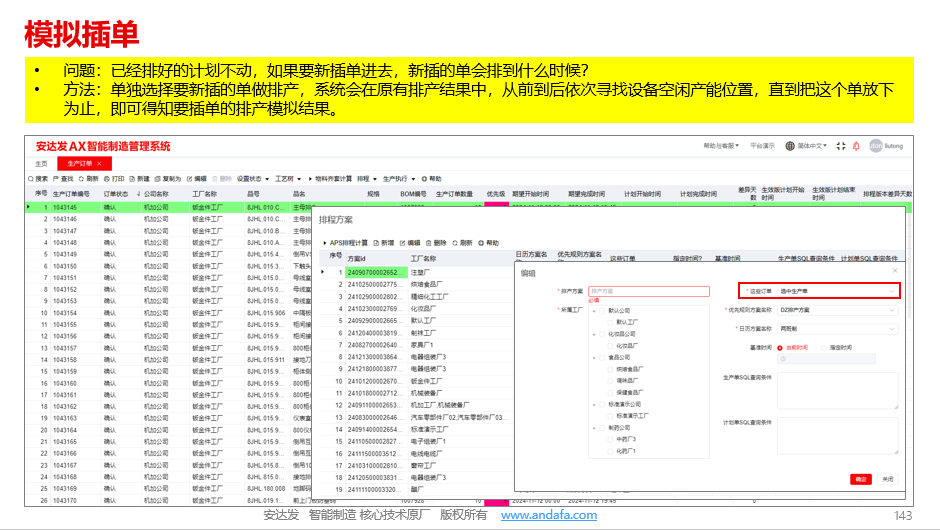
4. 能源成本精细化管控
针对电费占比高的痛点,APS生产计划排单软件支持分时电价智能排产,优先在低谷时段安排高能耗设备(如密炼机、硫化罐)的生产。部分系统还能结合模具生命周期管理,预测维护时间,避免非计划停机导致的能源浪费。
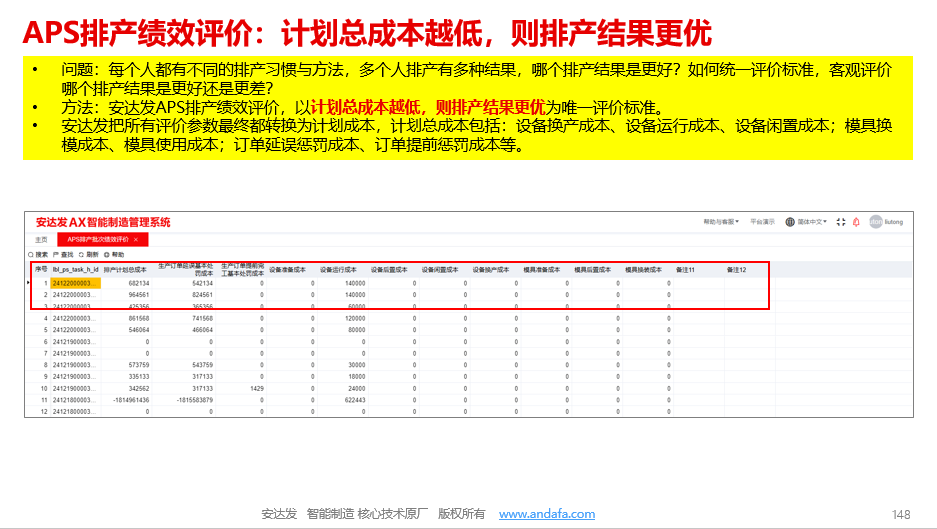
三、实施APS生产计划排单软件的长期价值
1.提升设备利用率:通过动态排程与冲突检测,设备闲置率可降低15%-20%。
2.缩短交付周期:订单合并与智能插单功能帮助平均交期缩短25%以上。
3.降低综合成本:减少换型
时间与能源优化可直接节约8%-12%的生产成本。
4.增强合规性:工艺参数的强制关联与预警机制规避了质量与合规风险。
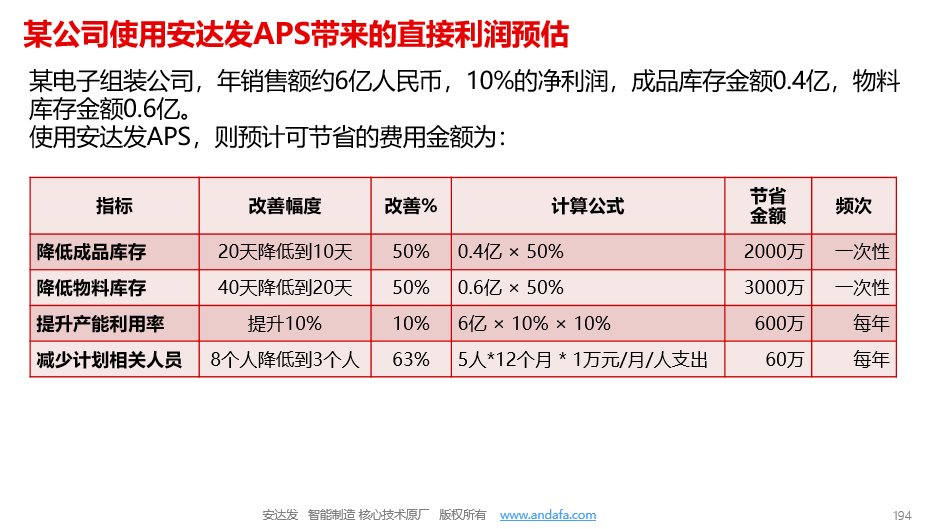
结语
塑胶行业的排产难题本质是复杂约束下的资源优化问题。APS生产计划排单软件通过工艺建模、智能算法与实时数据驱动,将传统“经验排产”升级为“计算排产”,不仅解决了设备冲突、插单混乱等短期问题,更为企业提供了持续降本增效的数字化基础。未来,随着AI技术与物联网的深度融合,APS生产计划排单软件将进一步推动塑胶行业向智能化、柔性化生产迈进。