安达发|电子行业APS生产计划排产软件:破解“短交期+多品种”生产困局的智能钥匙
在电子制造领域,“多品种、小批量、短交期”已成为行业常态,半导体、消费电子、汽车零部件等细分领域尤其突出。传统生产计划依赖Excel表格和人工经验,面对数百道工序、动态设备状态、紧急插单等复杂变量时,往往导致交期延误、设备闲置、库存积压等问题。据统计,这类低效排程每年吞噬企业30%以上的潜在利润。而APS(高级计划与排程)系统凭借实时数据整合与智能算法,正成为电子行业破解生产困局的核心引擎。

一、动态排程:从“经验驱动”到“数据驱动”
电子制造工艺复杂,例如SMT贴片需匹配200+工艺参数,CNC加工涉及钛合金等特殊材料的效率波动。传统人工排程难以应对以下挑战:
• 多约束冲突:设备维修与生产计划重叠、物料断供风险、人员技能错配等问题频发;
• 响应滞后:订单变更或设备宕机时,人工调整需数小时甚至数天;
• 资源浪费:某电子代工厂因排程不合理,关键设备闲置率高达40%。

APS生产计划排产软件通过实时抓取ERP/MES数据(如设备OEE、物料库存、工艺标准),构建“订单-物料-设备-人员”四维动态模型。例如,某汽车零部件企业每15分钟同步2000+数据节点,实现:
• 秒级响应异常:自动识别设备故障并生成替代方案,订单交付周期缩短40%;
• 智能冲突消解:采用“三阶决策树”算法,调用历史案例库匹配最优解,订单变更审批时间从3天压缩至4小时。
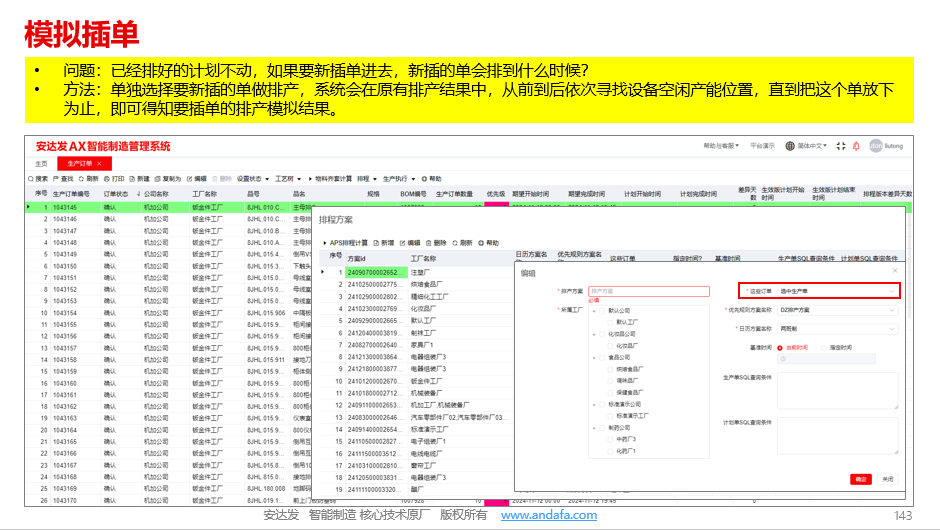
二、智能优化:平衡“交期、成本、质量”不可能三角
电子行业客户对交期准确性要求严苛,而生产成本与质量稳定性同样不可妥协。APS生产计划排产软件通过多目标优化算法打破这一僵局:
1. 优先级动态加权:某家电企业构建“订单价值系数=(交期紧迫度×3)+(利润贡献率×2)+(工艺复杂度)”,将5级优先级细化为12维动态权重,长单拆解为“主生产单元+卫星任务包”,交期达成率提升至92%;
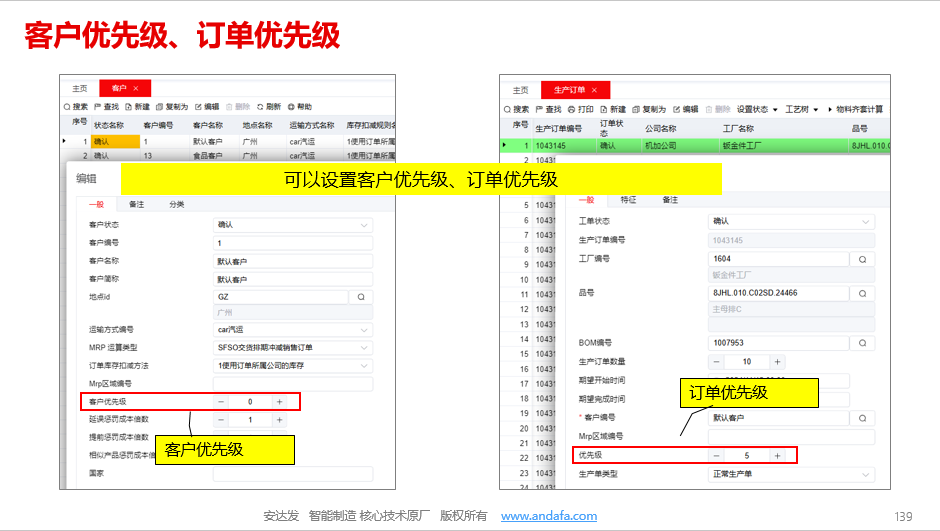
2. 资源精准匹配:通过“设备健康指数”模型监测主轴振动、液压压力等300+参数,智能推荐最佳“设备-物料-工艺”组合。某装备制造企业借此将OEE(设备综合效率)从68%提升至82%;
3. 库存成本控制:结合JIT(准时制)采购模块,原材料库存降低30%+。某半导体企业通过APS生产计划排产软件的72小时物料预警功能,避免500万订单延误损失。
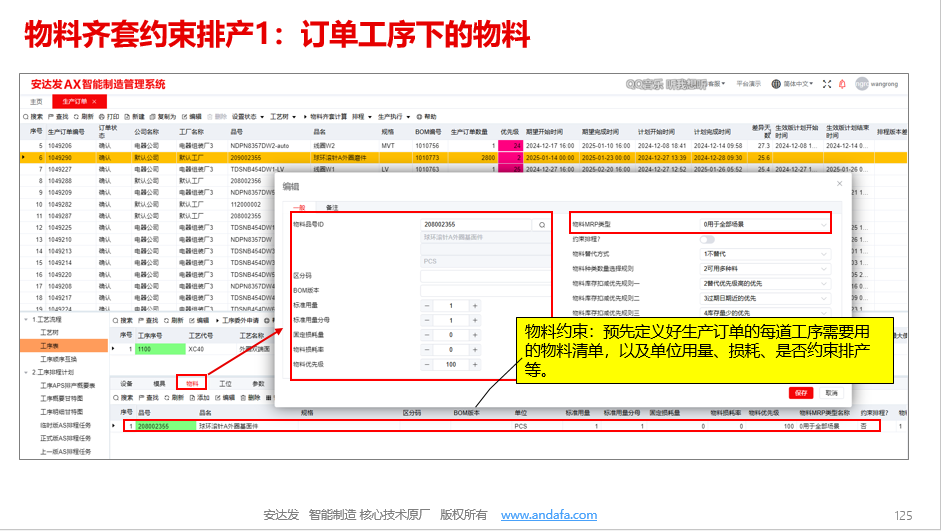
三、可视化与协同:构建敏捷生产网络
电子行业供应链波动频繁,APS生产计划排产软件通过以下能力增强企业韧性:
• 三维可视化看板:实时监控设备热力图、产能缺口雷达图,某注塑企业通过看板发现3台闲置机器,优化后排产提升15%利用率;
• 四级预警体系:从“蓝盾层”(14天物料监控)到“金刚罩”(跨厂区调度),某快消品企业2023年成功应对3次供应链中断;
• 数字孪生融合:虚拟产线映射物理世界,某飞机制造商计划调整响应时间从小时级降至分钟级,空闲产能发现效率提升300%。
四、未来展望:AI与自适应算法的深度赋能
随着AI技术发展,APS生产计划排产软件正迈向更高阶的智能化:
• 自适应学习:某服装企业通过AI预测使库存周转天数从45天降至28天;
• 新产品加速导入:数字孪生技术缩短试产周期60%,助力电子企业快速响应市场需求。
结语:在电子行业“短交期+多品种”的竞争中,APS生产计划排产软件已超越工具属性,成为企业实现“精准智造”的战略级解决方案。从动态排程到资源优化,从风险预警到AI赋能,这把“智能钥匙”正在打开电子制造高效、柔性、可持续的新未来。