安达发|从5天到2天:看APS智能排程如何改写食品包装交付规则!
引言:食品包装行业的交付困境
在快消品行业,包装交付速度直接影响产品上市节奏。然而,传统食品包装企业的生产排程往往依赖人工经验,面临订单波动大、换产频繁、交期紧张等挑战,平均交付周期长达5天甚至更久。如何缩短生产周期、提升准时交付率,成为行业亟需解决的难题。
安达发APS(高级计划与排程)系统的引入,正在彻底改变这一局面——通过智能算法优化生产调度,部分食品包装企业的交付周期从5天缩短至2天,效率提升150%,重新定义了行业交付标准!
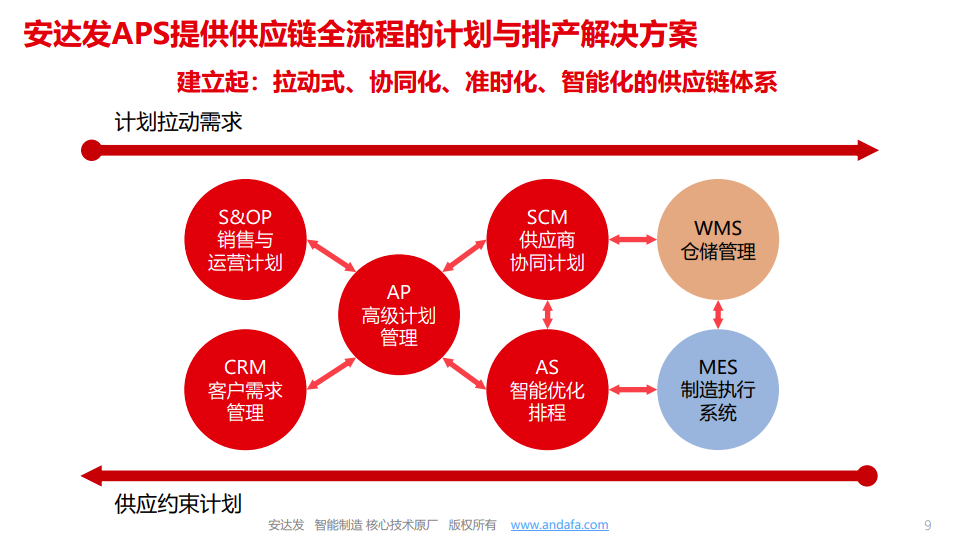
一、食品包装行业的排产痛点
食品包装生产具有多品种、小批量、高时效的特点,传统排产方式主要面临以下问题:
1. 订单波动大,计划赶不上变化
• 促销季订单激增,而淡季产能闲置,人工排产难以快速调整。
• 紧急插单频繁,原计划被打乱,导致交期延迟。
2. 换产效率低,停机损失严重
• 不同包装规格(如瓶装、袋装、礼盒装)需频繁更换模具和参数,每次换产耗时1-3小时。
• 缺乏优化排程,换产次数过多,设备利用率不足60%。
3. 资源冲突,生产瓶颈频发
• 模具、原材料、人员等资源调度不当,常出现“人等机”或“机等人”的情况。
• 部分产线超负荷,而其他产线闲置,整体产能无法最大化。
4. 依赖人工经验,排产效率低下
• 计划员靠Excel排产,计算复杂,调整一次计划需半天甚至更久。
• 缺乏数据支撑,排产结果往往非最优,导致产能浪费。
这些问题导致许多食品包装企业陷入“加班赶货仍延迟交付”的恶性循环,客户满意度下降,市场竞争力受损。
二、安达发APS生产排单软件如何实现交付周期减半?
安达发APS生产排单软件通过智能算法+实时动态优化,从生产排程的各个环节提升效率,最终实现交付周期的突破性缩短。
1. 智能订单分组,减少换产次数
传统排产按“先到先做”原则,导致换产频繁。而APS系统基于相似性算法,自动将相同工艺、相同模具的订单集中生产,减少切换次数。
案例:某饮料包装企业原每日换产12次,APS生产排单软件优化后降至5次,仅换产时间就节省7小时/天,相当于产能提升20%!
2. 动态优化排程,快速响应插单
当紧急订单插入时,传统方式需人工重新计算,耗时且易出错。而APS生产排单软件可在几分钟内重新排程,并自动评估对现有订单的影响,确保交期最优。
案例:某休闲食品包装厂应用APS生产排单软件后,紧急订单调整时间从4小时缩短至15分钟,插单交付准时率提升至95%。
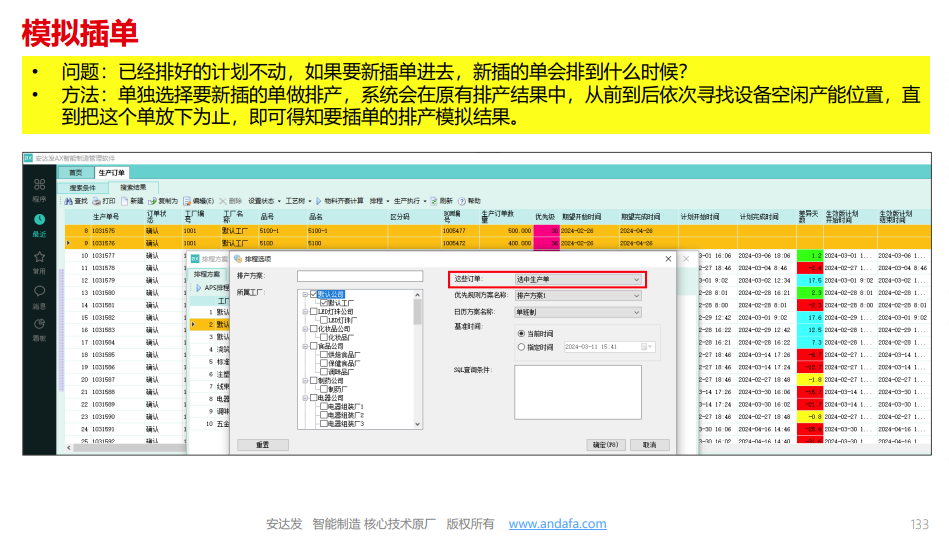
3. 资源智能匹配,消除生产瓶颈
APS生产排单软件实时监控设备、模具、原材料、人员等资源状态,自动匹配最优组合,避免资源冲突。
案例:某调味品包装企业通过APS生产排单软件优化模具调度,设备利用率从65%提升至85%,日均产量增加30%。
4. 可视化排产,提升协同效率
• 甘特图动态展示:计划员可直观查看设备负荷、订单进度,快速调整。
• 移动端实时监控:生产、采购、仓储等多部门协同,减少沟通成本。
案例:某乳品包装厂使用APS生产排单软件后,计划制定时间从2天缩短至2小时,排产效率提升10倍!
三、真实案例:从5天到2天,某龙头包装企业的蜕变
企业背景:国内某大型食品包装企业,主要客户包括知名乳品、饮料品牌,原平均交付周期5天,旺季时延期率高达40%。
APS生产排单软件应用效果:
1. 交付周期缩短60%:从5天降至2天,客户满意度大幅提升。
2. 换产时间减少70%:智能排程使每日换产次数从10次降至3次。
3. 产能利用率提升25%:设备闲置率降低,月均产量增长超1万吨。
4. 计划效率提高10倍:排产时间从1天缩短至1小时,人力成本降低。
该企业生产总监表示:“安达发APS生产排单软件让我们的交付能力从行业平均水平跃升为领先水平,客户订单量增长了30%!”
四、结语:效率革命,从智能排程开始
在食品包装行业,交付速度=竞争力。安达发APS系统通过智能优化排程,帮助企业实现从5天到2天的交付突破,彻底改写行业规则。
对于希望提升交付能力、降低生产成本的企业来说,APS生产排单软件已不再是“锦上添花”,而是生存与发展的必选项。未来已来,您的企业准备好迎接效率革命了吗?