安达发|APS排程软件让家电换型效率提升100%!智能排产助力制造业飞跃
引言:家电制造业的换型痛点
在家电制造行业,产品换型(即生产线从生产一种产品切换到另一种产品)是生产过程中不可避免的环节。然而,传统的换型流程往往效率低下,涉及设备调整、模具更换、工艺参数重置等多个步骤,导致停机时间长、产能损失严重。据统计,许多家电企业的换型时间占生产总时间的15%-30%,严重制约了生产效率和柔性制造能力。
如何缩短换型时间、提高设备利用率,成为家电制造企业提升竞争力的关键。而安达发APS(高级计划与排程)系统的引入,正在彻底改变这一局面——通过智能算法优化生产排程,部分企业的换型效率甚至提升300%,实现了惊人的生产优化!
一、传统换型管理面临的挑战
在家电行业,尤其是多品种、小批量生产模式下,换型频繁且复杂。主要问题包括:
1.换型时间长:传统依赖人工经验排产,换型顺序不合理,导致设备停机时间过长。
2.生产计划不稳定:急单插入、物料短缺等因素打乱原有排程,换型计划频繁调整。
3.资源冲突:模具、夹具、人员等资源调度不当,造成生产瓶颈。
4.缺乏数据支撑:换型时间、设备性能等数据未系统化管理,难以优化。
这些问题直接影响企业的交付周期、生产成本和市场响应速度。
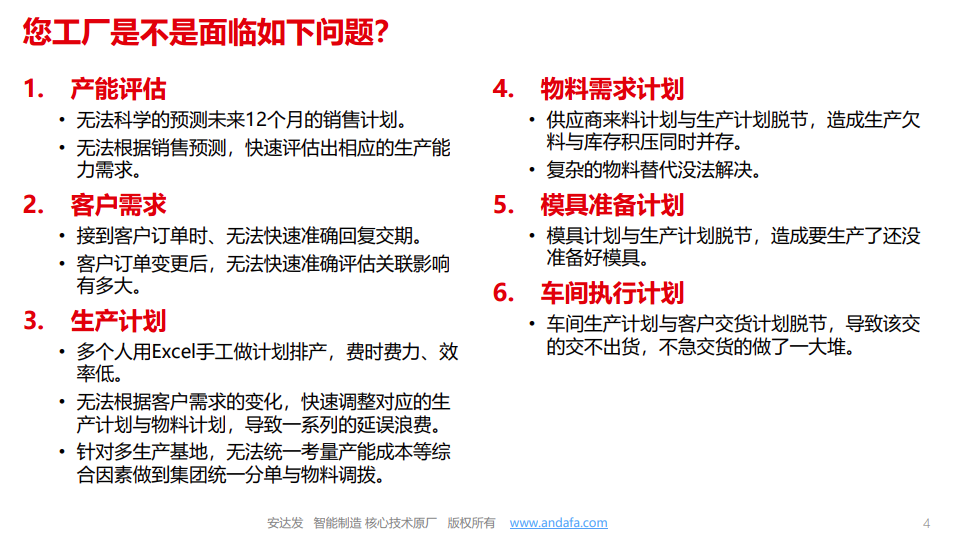
二、安达发APS排程软件如何实现换型效率飞跃?
安达发APS系统通过智能算法+大数据分析,从多个维度优化换型流程,实现效率的指数级提升。
1. 智能排产:减少换型次数,优化生产顺序
传统排产往往按订单先后顺序生产,导致换型频繁。而APS系统基于约束理论(TOC)和遗传算法,自动计算最优生产序列,将相同或相似工艺的产品集中生产,大幅减少换型次数。
例如,某家电企业原本每天需换型5次,每次耗时2小时,APS优化后换型降至3次,仅此一项就节省4小时/天,相当于增加10%有效产能!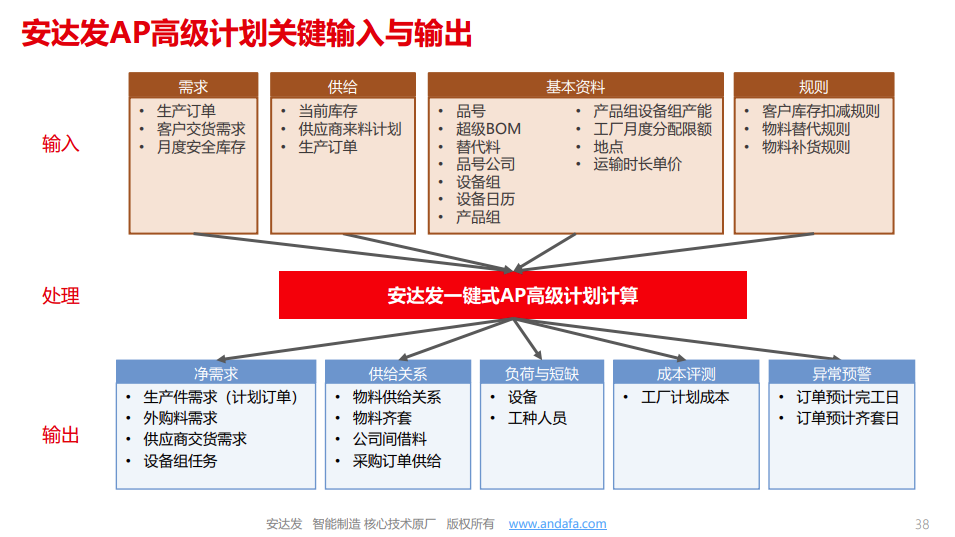
2. 换型时间标准化与动态优化
APS排程软件可记录历史换型数据,分析不同产品切换的标准时间,并自动优化换型步骤。例如:
•并行换型:在部分设备仍在生产时,提前准备下一产品的模具和参数。
•智能预警:系统自动提醒换型所需资源(如模具、工艺文件),减少等待时间。
某空调生产企业应用APS后,换型时间从120分钟缩短至40分钟,效率大大提升!
3. 资源协同调度,避免生产瓶颈
APS排程软件可实时监控设备、模具、人员的占用情况,自动匹配最优资源组合,避免因某一资源短缺导致换型延迟。例如:
•模具智能调度:系统自动匹配可用模具,并提前安排维护计划,避免临时故障。
•人员技能管理:根据操作员技能自动分配换型任务,减少人为失误。
某厨电企业通过APS排程软件优化模具调度,换型效率提升150%,模具利用率提高40%。
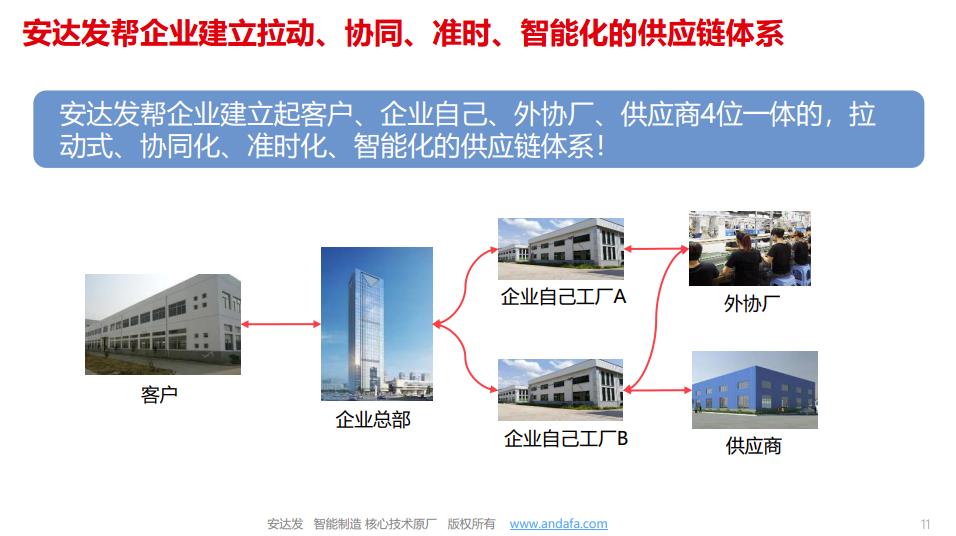
4. 实时动态调整,应对突发变化
生产过程中常遇到急单插入、设备故障等突发情况,传统排产需人工重新计算,耗时且易出错。而APS排程软件支持实时动态排程,在几分钟内重新优化生产计划,确保换型影响最小化。
某冰箱制造厂在引入APS排程软件后,紧急订单的换型调整时间从2小时降至30分钟,生产灵活性大幅提升。
三、真实案例:某家电巨头的效率革命
客户背景:国内某大型家电集团,产品涵盖冰箱、洗衣机、空调等,产线换型频繁,平均换型时间占生产时间的20%,严重影响交付能力。
APS排程软件应用效果:
1.换型时间减少70%:通过智能排程和并行换型优化,单次换型时间从90分钟降至30分钟。
2.产能提升30%:换型次数减少,设备利用率提高,月产量增加近1/3。
3.交付周期缩短40%:生产计划更稳定,订单准时交付率从75%提升至95%。
该企业生产负责人表示:“安达发APS排程软件让我们的换型效率提升80%,相当于在不增加设备的情况下,多出一条生产线!”
四、未来趋势:APS+工业互联网,打造智能工厂
随着工业4.0的推进,APS系统正与MES(制造执行系统)、IoT(物联网)、数字孪生等技术深度融合,实现更智能的换型管理:
•预测性换型优化:基于设备状态数据,预测最佳换型时机。
•自动化换型(SMED):结合机器人技术,实现快速自动换模。
•AI自主学习:系统不断积累换型数据,自动优化排产策略。
未来的智能工厂,换型将不再是生产瓶颈,而是高效柔性制造的核心竞争力!