安达发|橡胶制品APS排产:在弹性与刚性间缔造生产秩序
在泰国橡胶林的晨雾中,乳白色胶汁缓缓流入收集桶时,千里之外的橡胶制品工厂正经历数字化变革的阵痛。一家顶级轮胎制造商因硫化工艺排程失误,导致2000条子午线轮胎性能不达标,直接损失超500万元。这个典型案例折射出橡胶制品行业排产管理的核心矛盾:原材料的高度弹性与生产工艺的刚性约束。当新能源车用橡胶件需求年增45%、传统密封件市场萎缩20%的产业变局下,APS系统正成为破局关键。
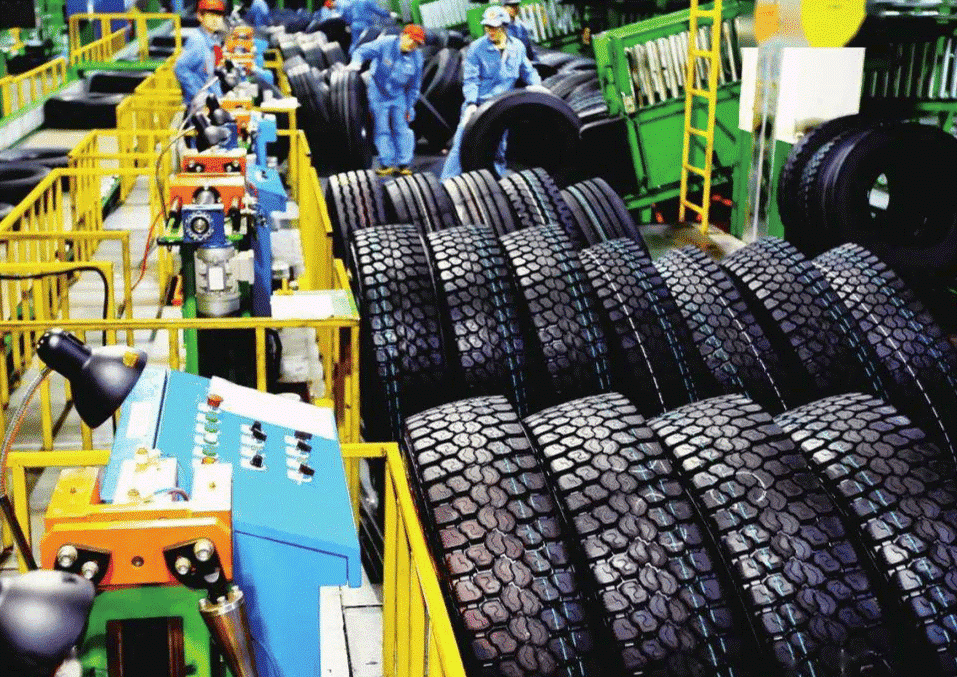
一、橡胶制品排产的特殊性挑战
工艺约束形成多重枷锁。在传送带生产车间,硫化机的温度曲线控制直接决定产品性能。某V带生产企业数据显示,不同规格产品硫化时间差异达300%,设备切换需经历2小时降温-升温周期。这种热力学特性使传统排产模式效率低下,设备利用率常年徘徊在65%以下。
原料特性颠覆线性排程逻辑。天然橡胶与合成橡胶的共混比例直接影响混炼工序时长,某密封件厂的实验表明,当NR/SBR比例从70/30调整为50/50时,密炼时间需延长40%。这种非线性关系导致传统BOM系统失效,亟需动态排程算法支持。
市场需求呈现冰火两重天。新能源汽车电池包密封件订单季度波动幅度达200%,而传统建筑减震垫需求持续走低。某跨国企业因未能及时调整EPDM与CR产品排产比例,导致价值300万美元的氯丁橡胶库存积压。这种结构性矛盾要求排产系统具备实时响应能力。
二、安达发APS系统的五大核心要素
工艺知识图谱构建 某轮胎企业将200种硫化配方、3000条工艺参数转化为数字孪生模型,使排产系统自动识别配方冲突。当夏季胎与雪地胎共线生产时,系统智能调整硫化温度曲线,避免胶料焦烧风险,良品率提升至99.2%。
动态约束计算引擎 采用模糊逻辑算法的排产系统,可同时处理设备状态、模具寿命、能耗限制等50余项约束条件。某输送带厂引入后,在电力波谷时段自动排产高能耗的压延工序,单月电费降低18万元。
弹性产能缓冲机制 头部企业设置10%的浮动产能池,通过APS系统动态调配。当汽车客户紧急追加30万件雨刮胶条订单时,系统在2小时内重组4条产线的模具排程,将交付周期压缩40%。
物料追溯闭环系统 RFID技术与APS的深度集成,实现从生胶入库到成品出库的全链路追溯。某医用橡胶厂借此将原料损耗率从5%降至1.8%,同时满足FDA 21 CFR Part 11合规要求。
能效优化决策模型 结合实时能源价格的智能排产,使某减震制品企业蒸汽能耗降低25%。系统自动将硫化工艺排至供热管网压力峰值时段,单条生产线年节省能源成本80万元。
三、智能化转型的三重突破
数据治理筑基 某老牌橡胶厂历时8个月完成设备联网改造,将194台服役超10年的密炼机接入系统。通过振动传感器捕捉转子磨损数据,使预防性维护准确率提升至90%,意外停机减少70%。
组织架构再造 设立跨部门的智能制造委员会,打破生产、采购、研发部门壁垒。某企业通过每日战情会机制,将订单变更响应时间从48小时缩短至4小时,客户投诉率下降65%。
人机协同进化 开发AR辅助排产系统,车间主任通过智能眼镜实时接收设备负荷预警。某工厂应用后,设备排程冲突减少80%,新晋计划员培养周期从6个月压缩至45天。
在碳中和目标驱动下,某企业通过APS优化再生胶使用比例,每年减少碳排放1200吨。这种绿色智造新模式,正在重塑橡胶制品的价值维度。当液态金属橡胶走向产业化,排产系统或将需要协调固态与液态并行的混合制造流程。这场发生在高分子世界的数字革命,终将推动传统橡胶工业完成"弹性蜕变"。