安达发|降本增效新思路:橡胶塑料企业如何构建智能生产排程排产体系?
橡胶塑料行业作为典型的流程型制造业,其生产管理面临多品种、小批量、工艺复杂等挑战。传统的排产方式依赖人工经验,常出现设备利用率低、订单延期、库存积压等问题。随着智能制造的发展,橡胶塑料企业亟需通过数字化手段优化排产计划管理,以提升生产效率、降低运营成本并增强市场竞争力。本文将探讨橡胶塑料企业如何借助智能化排产工具和精益管理方法,实现生产计划的高效优化。
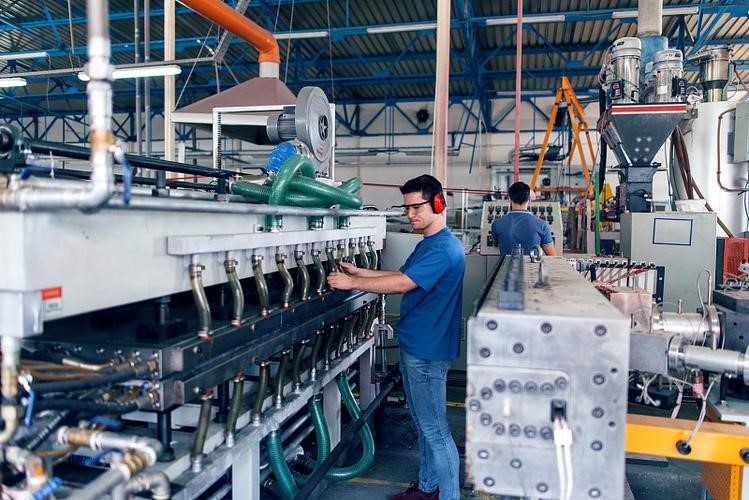
一、橡胶塑料企业排产管理的主要痛点
1、多品种小批量生产,换模频繁
橡胶塑料制品通常涉及多种配方、模具和工艺参数(如注塑、挤出、吹塑等),切换生产时需频繁调整设备,导致停机时间增加,影响整体生产效率。
2、订单交期波动大,插单频繁
客户需求多变,紧急订单和临时变更较多,传统排产方式难以快速响应,容易导致生产计划混乱,影响准时交付率。
3、设备利用率低,产能浪费
由于排产不合理,部分机台超负荷运转,而部分设备闲置,整体OEE(设备综合效率)较低,影响企业盈利能力。
4、库存管理困难,资金占用高
原材料(如橡胶、塑料粒子)和半成品库存管理不善,容易造成呆滞料或短缺,增加仓储成本和资金压力。
二、智能化排产优化策略
1、引入APS(高级计划与排程)系统
APS高级排程可基于实时数据(设备状态、物料库存、订单优先级)自动生成最优排产方案,解决传统人工排产的不足:
• 自动优化生产顺序:减少换模时间,提高设备利用率。
• 动态调整排程:遇到插单或设备故障时,快速重新计算生产计划。
• 可视化排产看板:直观展示机台负载、订单进度,便于管理人员决策。
案例:某塑料包装企业引入APS高级排程后,换模时间减少30%,订单准时交付率提升至95%。
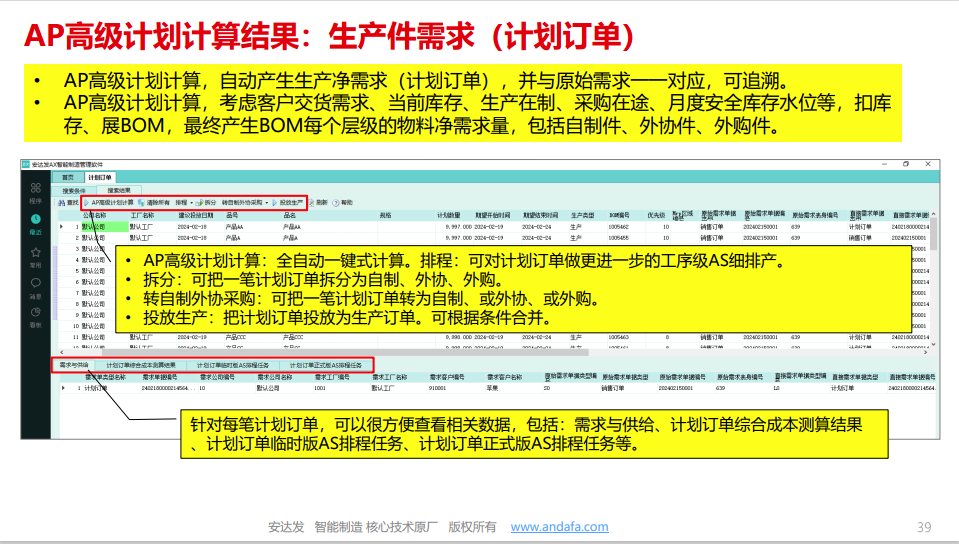
2、应用MES(制造执行系统)实现实时监控
MES系统可采集生产现场数据(如机台状态、良品率、工时统计),并与APS高级排程联动,实现:
• 实时生产跟踪:监控每个订单的生产进度,及时发现异常。
• 质量追溯:记录工艺参数,便于分析不良品原因。
• 绩效分析:统计设备OEE、工人效率,优化资源分配。
3、数据驱动预测排产
利用历史订单数据、市场需求趋势,结合AI算法进行:
• 需求预测:提前调整生产计划,避免旺季产能不足。
• 智能排产仿真:模拟不同排产方案,选择最优解。
• 供应链协同:与供应商共享排产计划,确保原材料准时到货。
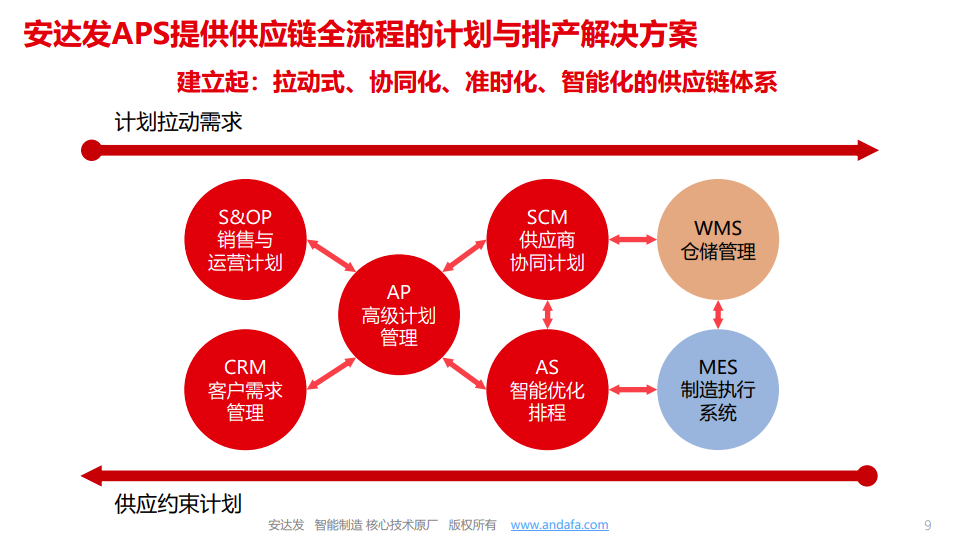
三、实施APS生产计划排产软件的效益
1、提升生产效率
• 减少换模时间,设备利用率提高20%-30%。
• 优化生产顺序,缩短订单交付周期。
2、降低运营成本
• 减少库存积压,资金周转率提升。
• 避免生产异常导致的废品和返工。
3、增强市场响应能力
• 快速应对插单和变更,提高客户满意度。
• 通过数据分析优化产品结构,提升竞争力。
四、成功案例
某汽车橡胶配件企业的生产计划排产实践
• 挑战:订单波动大,换模频繁,准时交付率仅75%。
• 解决方案:
1. 部署APS+MES系统,实现自动排产与实时监控。
2. 推行SMED,换模时间减少50%。
3. 应用AI预测需求,优化采购计划。
• 成果:设备OEE提升25%,订单交付率提高至98%,年节省成本超200万元。
橡胶塑料企业要实现高效排产管理,需结合智能化工具(APS、MES)和精益方法(SMED、JIT),构建柔性化生产体系。未来,随着工业互联网和AI技术的深入应用,排产优化将更加精准和自动化,助力企业实现降本增效和数字化转型。