安达发|当下99%的传统制造业遇到的排产问题?
在数字化转型浪潮下,传统制造业仍面临严峻的排产挑战。据调研显示,98%的传统制造企业在生产计划与排程环节存在明显痛点,这些问题直接影响交付能力、成本控制和市场竞争力。本文系统梳理当前主要排产难题,并探讨可行的解决方案。
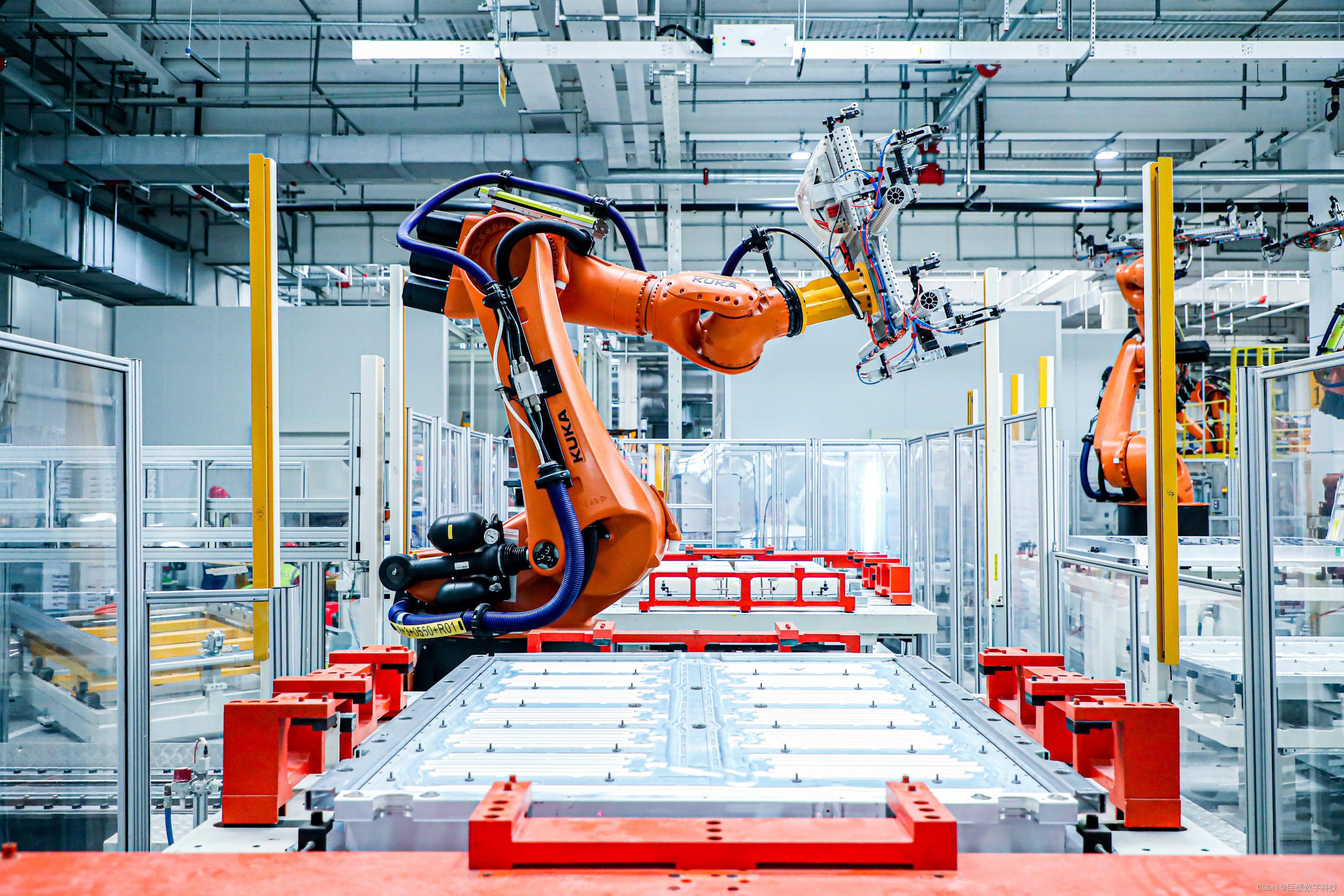
一、核心排产问题分析
1.信息孤岛严重
•生产数据分散在ERP、MES、Excel等多个系统
•设备状态、物料库存等信息无法实时同步
•某机械加工厂因数据不同步导致30%排产计划需要返工
2.动态响应滞后
•人工排产调整平均需要4-8小时
•紧急插单导致60%的原计划需要变更
•某汽车零部件企业每月因计划变更损失80万元
3.资源利用率低下
•设备综合效率(OEE)普遍低于60%
•换型时间占生产时间的25-40%
•某电子厂仅因换模问题每年多支出150万元
4.多约束条件冲突
•同时考虑设备、人员、物料等20+约束条件
•人工排产难以找到最优解
•某装备制造企业因排产不合理导致交付延期率达35%
5.供应链协同困难
•70%企业存在供应商交付不准时问题
•库存周转率比标杆企业低40-50%
•某家电企业因供应链问题每年多承担300万资金占用
二、问题根源探究
1.管理方式落后
•仍采用Excel手工排产占比高达75%
•计划员80%时间用于数据处理而非优化
2.系统支撑不足
•仅有12%企业部署专业APS系统
•现有ERP排产模块满足率不足30%
3.人才短板明显
•具备专业排产技能人员占比不足5%
•新老员工知识断层严重
4.标准化程度低
•工艺路线标准化率平均仅45%
•基础数据准确率普遍低于70%
三、典型行业痛点
1.离散制造领域
•多品种小批量特征明显
•某机床企业产品组合达2000+种
•计划复杂度呈指数级增长
2.流程制造领域
•设备连续运行要求高
•某化工厂因排产不当年损失800万
3.混合制造领域
•离散与流程生产并存
•某食品机械企业换产效率低下
四、解决方案建议
1.数字化升级路径
•实施专业APS系统(初期投入约50-100万)
•建立统一数据中台
•某零部件企业数字化改造后计划效率提升300%
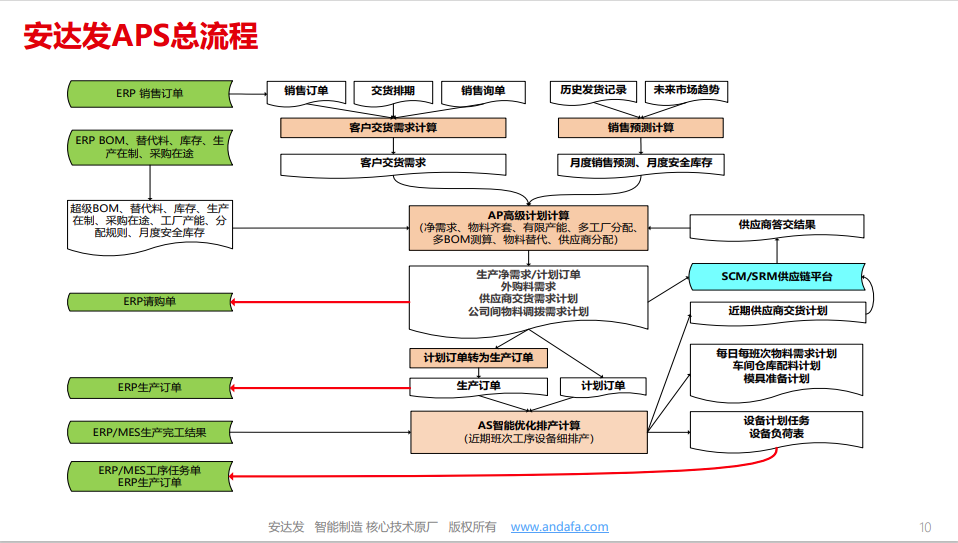
2.管理优化措施
•建立标准化工艺库
•推行精益生产方法
•某卫浴企业通过优化年节省200万
3.人才培养策略
•建立计划员认证体系
•引入智能制造课程
•某集团培训后计划质量提升40%
五、实施效益预测
1.直接经济效益
•计划效率提升50-80%
•库存降低20-30%
•交付准时率提升至95%+
2.管理效益
•决策时间缩短70%
•异常响应速度提升5倍
•员工满意度提高30%
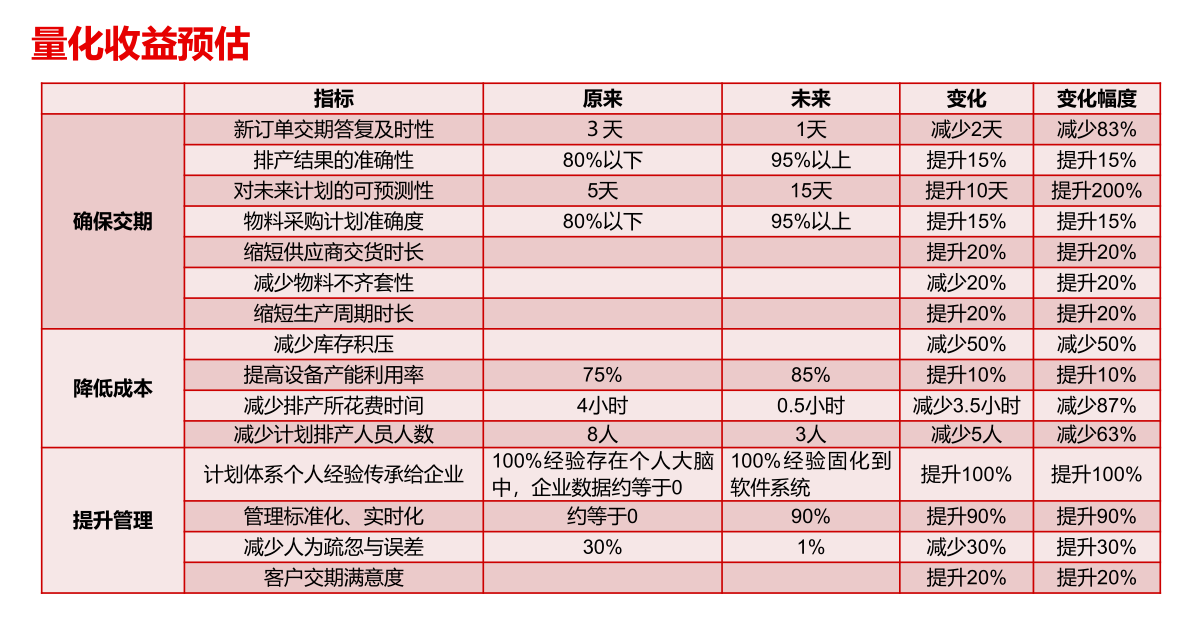
结语
传统制造业排产问题已成制约发展的关键瓶颈。通过"数字化工具+管理优化+人才培养"的组合策略,企业可在6-12个月内显著改善排产水平。建议企业根据自身情况,选择合适切入点启动改造,逐步构建智能排产能力,在激烈市场竞争中赢得先机。