安达发|电子产品生产中遇到的痛点APS系统如何解决
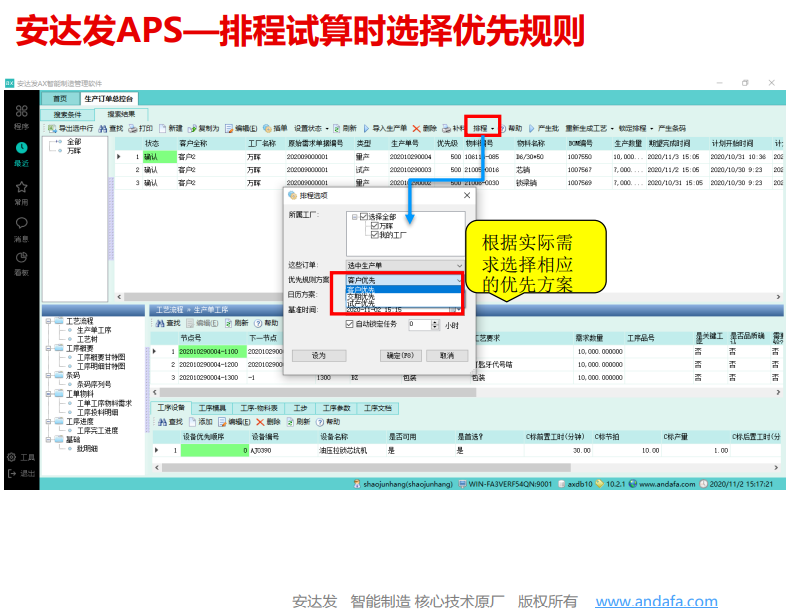
痛点一:精细化管理难,产品难追溯:
PCB制造还是基于批量加工管控,过程控制点均靠人员进行点检、识别和记录,过程无法将人机料法环测信息有效协同,产品加工信息纸档记录分散,查找效率低,追溯难。
痛点二:订单小品种多,计划排产难
随着市场需求模式的改变,PCB产品加工逐步向小批量多品种的定制化模式转变,由此生产计划排程越来越难,计划性差。
痛点三:设备多管理难,故障难预防
PCB制造的流程长,涉及的设备种类众多、数量也多,设备管理人员基于传统的管理方式,难以对设备状态进行有效监控,预防性保养维护难,故障难预防。
痛点四:制造过程复杂,工序难管理
PCB产品属于定制化加工,制造流程长,涉及设备种类多,管控点多,工序内需要进行计划及人机料法环测的多方面管控,管理难度大。
APS系统如何解决这些痛点:
1. 提高生产效率和设备利用率
- 即时准确的交期预测:APS系统能够在接到新订单时,即时准确地预测出其交期。这意味着企业可以更快地响应市场需求,减少因交期延误而造成的损失。
- 优化生产计划:当产线、机台、模治具、人力、物料等影响生产计划的因素发生变更后,APS系统会自动重新修正原有计划,确保生产活动能够顺利进行。
- 减少停机换产损失:通过充分利用设备产能,APS系统有助于提高设备利用率,从而减少因停机换产而造成的损失。
2. 降低库存成本和提高仓位利用率
- JIT式采购:APS系统支持JIT(Just-In-Time)式的采购,这有助于减少物料库存积压,降低长期采购资金的占用。
3. 减少人力资源成本
- 自动化流程:APS系统可以显著降低计划人员工作量,从而降低人力成本。
- 标准化管理:个人经验可以通过APS系统传承给企业,使管理标准化、系统化,减少人为疏忽与误差导致的一系列后果。
4. 提升数据分析能力
- 产销协同模式变革:APS项目的运行使用引入了MDS主需求计划的概念,建立了基于APS-MDS的产销协同模式,增强了数据分析能力。
- 电子料齐套分析变革:APS电子料齐套分析模型的使用,打破了之前手工分析存在的流程节点繁琐、人工操作多、分析时间长等局限。
5. 实现智能制造和工业4.0
- 实时监控与优化:APS系统对所有资源进行同步及实时监控,通过复杂的智能化数学算法,反复模拟、试探、优化、计算,最终生成一个新的、有效的、精确的、可执行的生产计划。
- 协调管理ERP和MES:APS是实现ERP和MES之间协调管理,避免信息孤岛的核心系统。
6. 精细化生产计划
- 有限资源能力的优化计划:不同于ERP系统的无限资源假设,APS是基于有限资源能力的优化计划,这使得生产计划更加实际操作性。
- 最优任务安排:APS系统解决了“先做什么,后做什么”的问题,确保在约束条件下(时间、场地、设备能力等)实现交货期、最低成本等最优。
7. 案例分析
- 电子生产中的排程问题解决:通过导入APS系统,包括新桥、太仓两地工厂的案例显示,APS助力智能化排产,成功一块复制一块,提高了主需求计划(MDS)和主生产计划(MPS)的效率。
此外,在深入分析了APS系统如何解决电子产品生产中的痛点之后,可以看到,APS系统通过其高级的计划与排程能力,为企业带来了诸多益处,包括提高生产效率、降低成本、提升数据分析能力以及实现智能制造等。这些优势使得APS系统成为电子产品生产企业应对市场变化、提高竞争力的重要工具。
APS系统的应用不仅解决了电子产品生产中的多个痛点,还为企业带来了更高的生产效率、更低的运营成本和更强的市场竞争力。随着智能制造和工业4.0的发展,APS系统的作用将变得更加重要,成为企业不可或缺的一部分。