安达发|某大厂使用APS计划排程真实成功案例
在很多群里、朋友圈、公众号上可以看到,很多精益咨询老师认为,不仅ERP不啥用,APS更是无聊之举,而且肯定是用不好的。但,事实上可能还真不是这样的。
一个深圳的客户,用了APS以后,不仅装配的齐套性大幅度增加,而且零件的库存也得到了大幅度的提高,而且准交率更是得到有效提升。
该客户的业务过程是比较复杂的:零件加工有8个车间(并行),装配及后加工有四个车间,一共有12个车间。8个并行的零件加工车间,都是多工序、多资源且换型复杂的生产过程。12个车间,大约有2000台加工设备,其中需要排程的机台超过600以上。产品有单个包装,有成套包装。且批量大小不一,交期长短不一,插单也比较频繁。还有更加麻烦的是,很多物料是需要进口的,是长周期物料,需要从国外进口,有批量、前置期的要求。
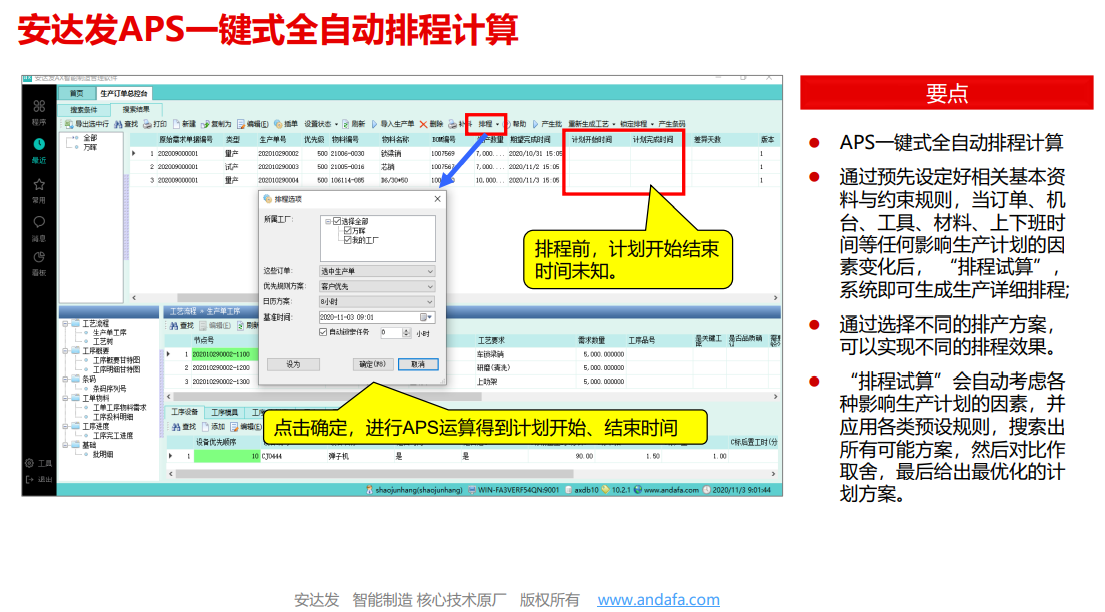
哦,需要说明的是,产品还是比较复杂的,一个产品的BOM用量基本上在50-60以上,齐套性有足够的要求。
这样的业务特征,手工计划和排程时非常麻烦的。虽然经过多次的布局优化、超市、现场5S等改善,而且所费资金也不少,但是交付和库存问题,远远得不到解决。
为了解决交付和库存问题,2021年开始上线APS系统:
一、MRP优化
由于ERP中MRP使用的便捷性不佳,不能符合现有的业务场景,所以首先是是定制了MRP系统,以满足业务需求。
定制的MRP系统,首先是实现了套装的分解,即套装成品分解为单品包装成品,再分解为零件等。其次,是成品、零件不同生产任务拆分和合并。成品的分拆需要满足一个Cell的经济批量,而零件加工则需要合并为比较大的批量生产,以减少换型。其三,在此基础上,计算净需求。
二、装配齐套排程
销售订单根据MRP分解为生产任务后,对装配进行多产线(并行产线100条以上)的在库、在途、采购前置期的齐套排程。
装配车间完全按照APS的排程执行,确保成品任务满足订单发货的需求。
三,零件加工顺序排程
由于零件生产过程更加复杂,工艺路线、标准工时等等需要足够多的数据准备,先按照装配齐套要求,按照装配的开工日期拉动生产(无限产能排程),确定零件生产的顺序。各个零件生产时,按照确定的优先顺序生产即可。
经过一年多的实际运作,效果如下:
第一,所有的采购件、自制件的数量,完全采用MRP计算结果。系统算是多少就是多少,不做人工干预。
第二,整改工厂完全适应了装配APS详细排程、零件生产顺序生产的业务模式。且PMC部门等等已经无法返回到手工状态。
第三,装配所需要的零件大幅度降低(现有库存面积会原有的40%,即库存降低了60%),齐套性还大幅度增加。仅仅会出现少量的断料现象(零件加工车间,实际产出时间,超过了前置期的时间,个别零件加工车间不按照顺序生产)。
第四,准交率上升和交付能见度增加。APS详细排程后,完全按照销售订交期的紧急程度排程,即,紧急优先。准交率从原来是60%-70%提高到80-90%,提高了20%以上。更加重要的时,由于是对每个销售订单的成品任务进行详细排程,可以预支销售订单的齐套时间(注意,订单成品的齐套时间,多型号发货的),消除了客户对产品交付的焦虑,客户关系得到了良好的维护。
所以,在不改变现有做法的状况下,通过APS软件赋能生产计划过程,还是可以取得非常好的效果。
在MRP、APS成品齐套排程的基础上,正在进行零件生产的关键工序详细排程和销售订单交期自动评审的推动工作。