APS智能排产助食品制造加工企业提升生产管理?
最近,某品牌月饼吃出塑料纸的新闻登上热搜,在该事情得到发酵后,品牌发声明表示,接到投诉后已第一时间顾客取得联系,并针对此事件的专项检查正在进行。除了此次月饼被吃出塑料的问题外,在某一投诉平台上,有关于该品牌的食品安全问题的投诉数量已经高达一千六百多起,在质疑声中,该品牌的股价不断走低。
食品制造加工企业质量问题的频发,必定会导致消费者对企业的信任下降,从而导致口碑下滑,订单减少,甚至可能导致企业亏损、倒闭。
食品企业食品安全问题频发,主要有这三点:
一.生产工艺及环节没有一个系统化的管理。
传统的生产通常是采用人工的形式,生产工艺及环节没有进行数据系统化,容易让产品在生产过程中,因某一工艺的缺少导致质量问题的产生。
二.生产人员没有经过系统化的培训。
由于企业生产工艺没有一个标准化的管理,容易导致企业关键生产的人员离开后,技艺出现丢失,再加上人员的流动性较大,企业难以对新员工进行一个系统的生产技能培训,进而导致因人为随意性的产品质量问题产生。
三.追求利益忽视消费者健康。
企业的生产是为了满足消费者需求实现盈利的一种经济活动,由于消费者对食品安全的重视,使得企业需要生产健康无害的产品,但健康无害的食品生产往往涉及到巨大的成本,有些经营者会为了追求高额的利润,往往进行低成本的生产导致质量、健康安全问题的产生。
总而言之,食品生产质量问题的产生多归结于企业生产管理的不规范,企业如何使用APS智能排产提升生产管理?
APS智能排产可以实现企业生产资源的约束,将生产工艺系统化,减少因人为随意性可能导致的问题,降低企业的成本,提升企业的生产管理效益。
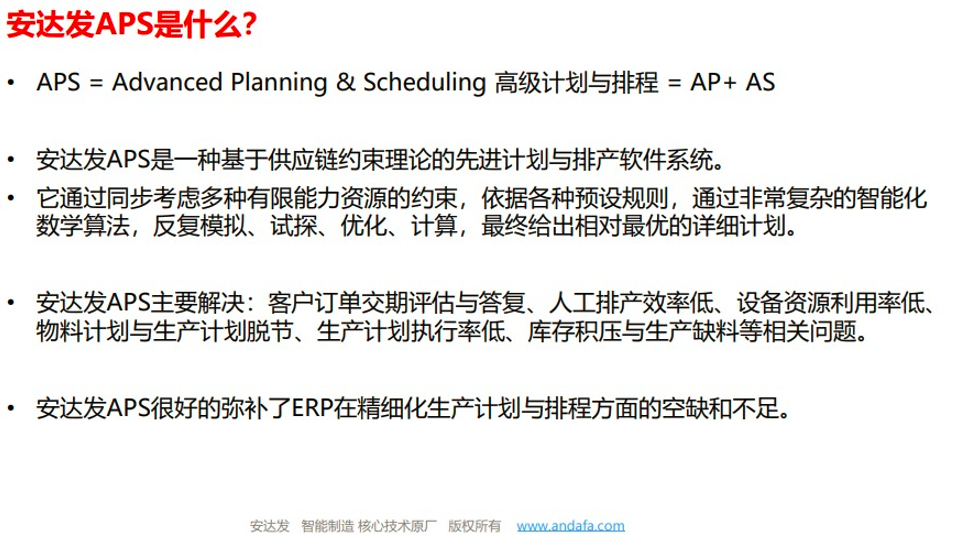
APS智能排产通过销售预测、物流运输计划、生产需求计划、智能优化排产、高级物料需求计划及供应商交货计划,提供企业供应链全流程计划与解决方案,实现交货需求、生产计划、采购计划、自制件、外购件的拉动式协同供应,从而显着减少交期延误、库存积压、与生产欠料等重大问题。
APS智能排产主要采用工艺流程基础数据与资源约束、订单级的优先选择规则方案、工序优化规则来实现排程结果的最优化:
- 在产品工艺中,我们预先定义好每个产品工艺流程中每个工序的资源与特征约束,包括工序资料、特征、可用 机台产线、模治具、物料、时间等,由此实现工艺的基本资源约束。
- 我们把所有待排程订单按紧急程度分为3大类:特急、一般、不急,并针对每种紧急程度分别设置具体的排序 选择规则,由此实现大范围的急单先做的效果。
- 我们针对每个工序详细设置其优化规则,如少换产、少换模、少换料、少换规格、按某个特征从小到大从大到 小等。并对短期的排程结果进行优化,由此实现机台产线的尽量连续生产,从而显着减少换产带来的工时和物料损失。
APS智能排产不仅可以实现普遍的资源约束,另外还提供多种手工调整的方法,可灵活的对排程结果做可视化的拖动调整,从而实现了个别个性需求的灵活处理。
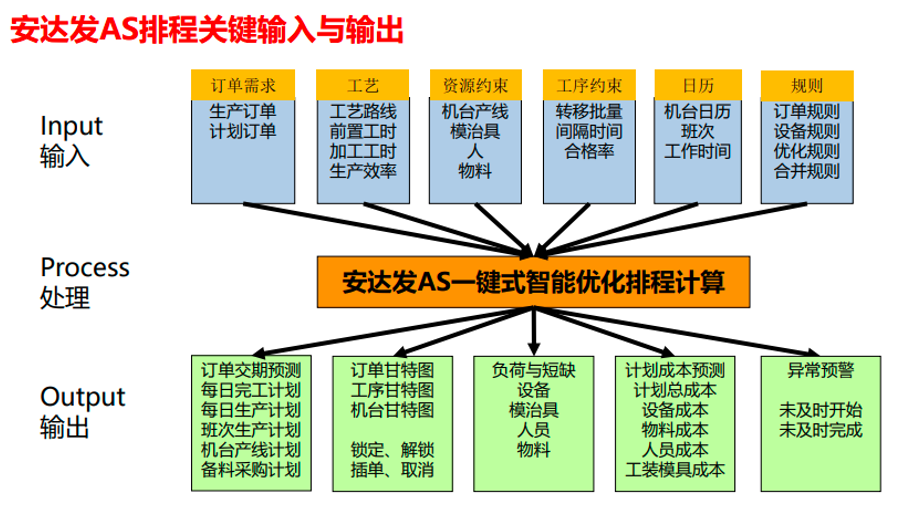
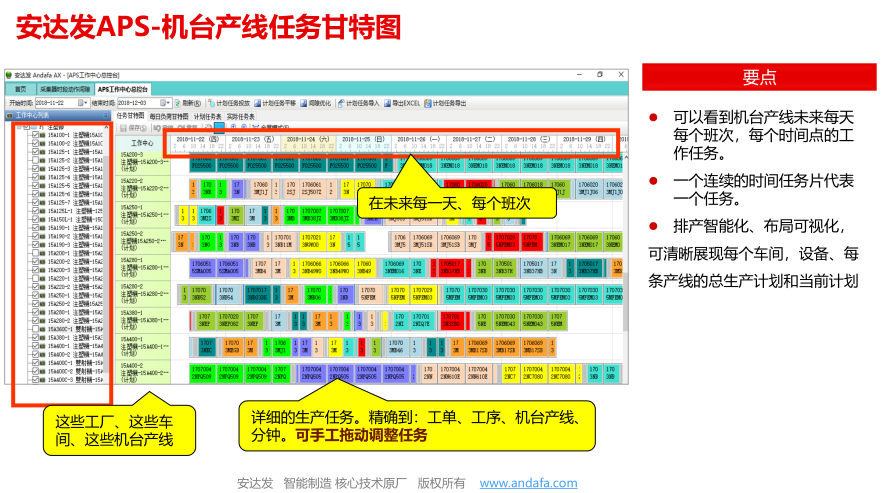
APS智能排产依靠严谨的数据及逻辑运算,短时间内自动分解长期计划到日计划(短期内车间产线机台精细化排产),可以实现多任务工序前后联动,并自动扣减完工数和库存,最后产生多种直观化报表,帮助企业进行决策。
食品制造企业可以使用APS智能排产实现企业生产工艺的标准化,实现生产的规范性,减少人为错误而造成的损失,让企业的生产管理更加高效。