APS智能排产帮你解决排产难题
随着市场经济的发展,人们对于消费的需求越来越多样化,导致产品越来越多样化、精细化,由于消费者对产品的种类、品质等要求越来越高,企业的生产排产难度也逐渐加大,再加上生产过程中可能会面临多种因素的变化,这让企业的生产排产难度更加的大。
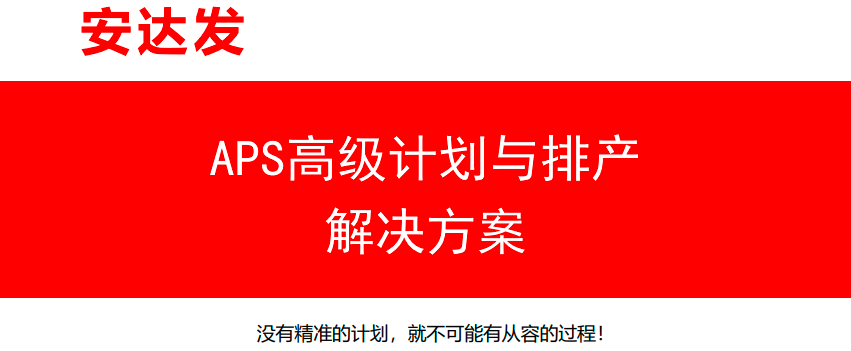
早期的制造企业基本上是采用手工Excel进行生产计划的排产,可是随着企业的发展逐渐发现Excel需要消耗大量的人力精力,导致企业的运营成本上升,随着ERP系统的出现,多数企业都引入了ERP系统,随着消费者对于产品的需求越来越多样化,对品质的要求也越来越高,ERP系统的短板也露出来了:
- 无法准确回复客户订单交期;
- 通过Excel做生产计划排产,而且面对生产要素变化时无法做到及时调整生产计划;
- 无法与供应商及时沟通,可能导致物料供应不及时,造成生产缺料、库存占用大;
- 设备使用及保养计划无法和生产计划匹配;
- 车间生产计划混乱,可能导致交不出货或生产货物过多,造成产品堆积;
- 盲目生产,生产过剩导致库存积压。
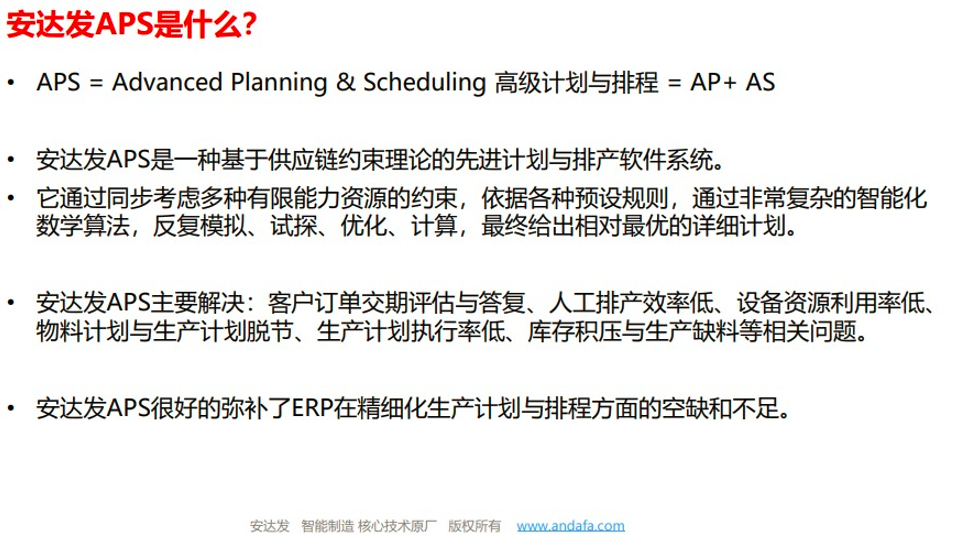
AP智能排产可以考虑客户订单、销售预测交货计划、库存等通过AP工厂高级计划产生每个工厂的未来的生产净需求量,即计划订单,并根据有限产能约束,通过AS车间优化排产进行短期内车间产线机台精细化排产。
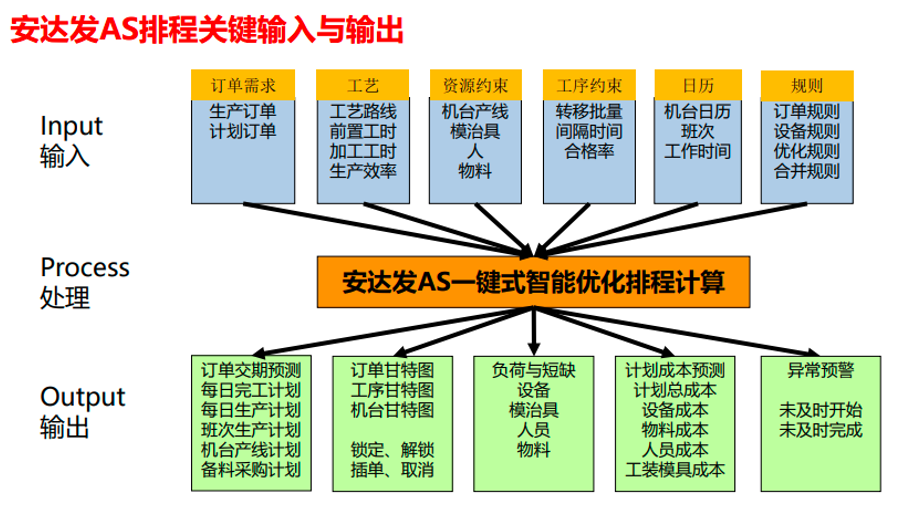
APS智能排产通过在全自动计算过程中同时应用如上3种方法,就实现了普遍的约束与优化。另外我们提供多种手工调整的方法,可灵活的对排程结果做可视化的拖动调整,从而实现了个别个性需求的灵活处理:
- 工艺流程基础数据与资源约束:在产品工艺中,我们预先定义好每个产品工艺流程中每个工序的资源与特征约束,包括工序资料、特征、可用 机台产线、模具、物料、时间等,由此实现工艺的基本资源约束。
- 订单级的优先选择规则方案:我们把所有待排程订单按紧急程度分为3大类:特急、一般、不急,并针对每种紧急程度分别设置具体的排序 选择规则,由此实现大范围的急单先做的效果。
- 工序优化规则: 我们针对每个工序详细设置其优化规则,如少换产、少换模、少换料、少换规格、按某个特征从小到大从大到小等。并对短期的排程结果进行优化,由此实现了机台产线的尽量连续生产,从而显着减少换产带来的工时和物料损失。
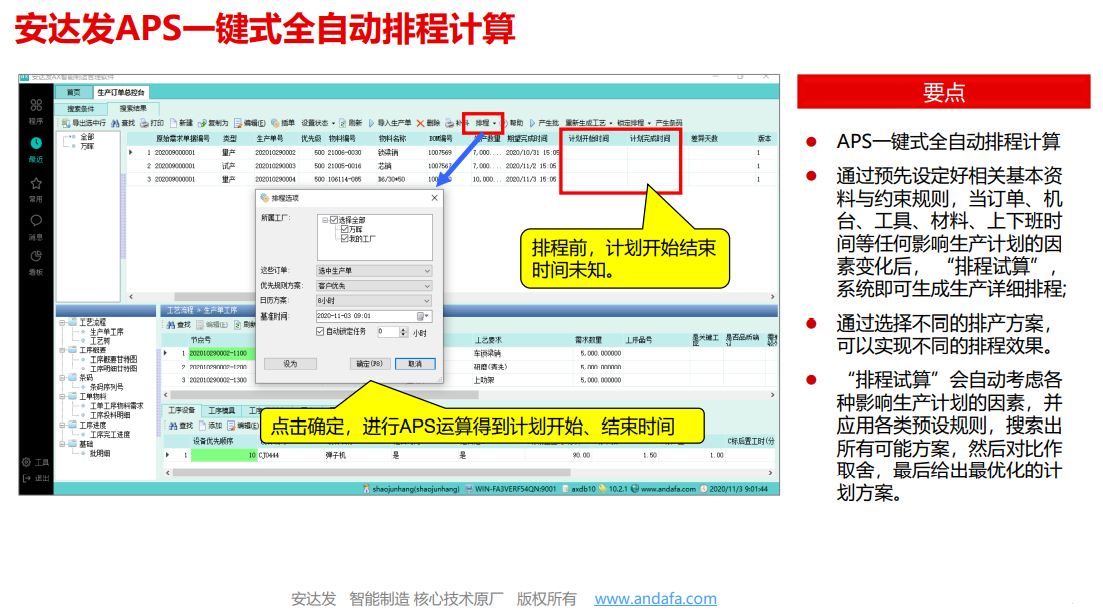
APS智能排产有着基于计划排产的AMRP高级物料需求计划及智能优化的车间排产,灵活滚动式的订单交货计划、生产计划,通过计划订单、详细生产计划、外购料需求计划及交货计划与生产计划,实现企业的自动智能化排产,实现交货需求、生产计划、采购计划、自制件、外购件的拉动式协同供应。